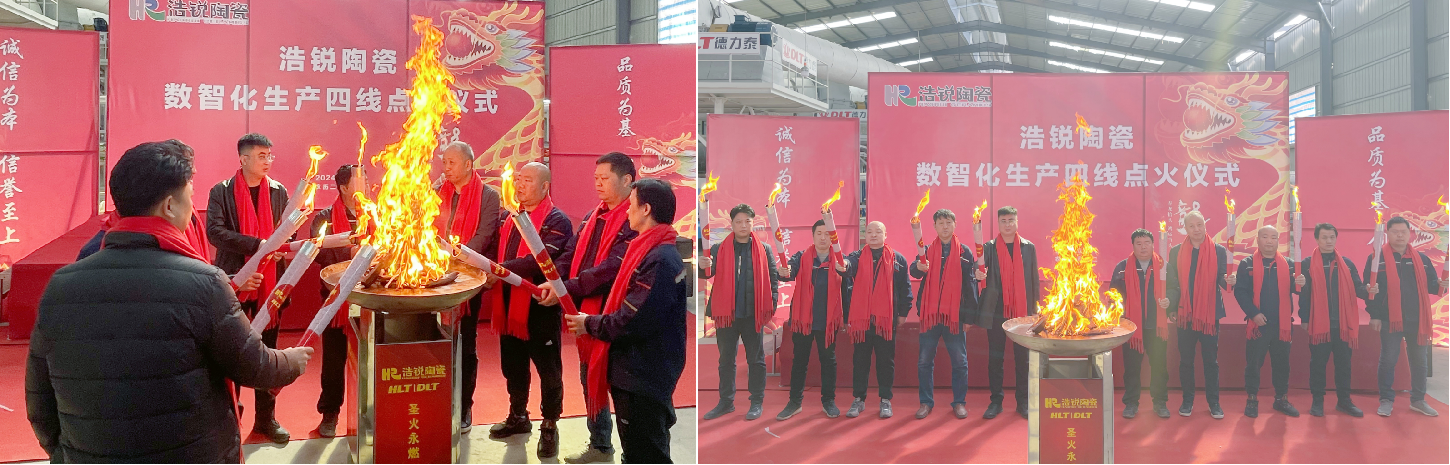
Established in 2013, Haorui Ceramic has always adhered to high standards and strict requirements for machinery manufacturing and product quality. With independent brands such as "Taihang Star" and thirteen series including 800*800mm polished tiles in over a hundred varieties, it is an outstanding ceramic enterprise with extensive influence in Hebei and even the northern production area in China.
Emphasizing development with high quality as its theme, Haorui Ceramic actively seeks new paths of transformation and upgrading according to market changes. While upgrading its existing products, it has invested in the construction of the fourth modern full-polished glaze complete production line. The first high-end large slab intelligent production line, a collaboration with HLT&DLT (consisting of three lines), was successfully put into operation in March 2023.
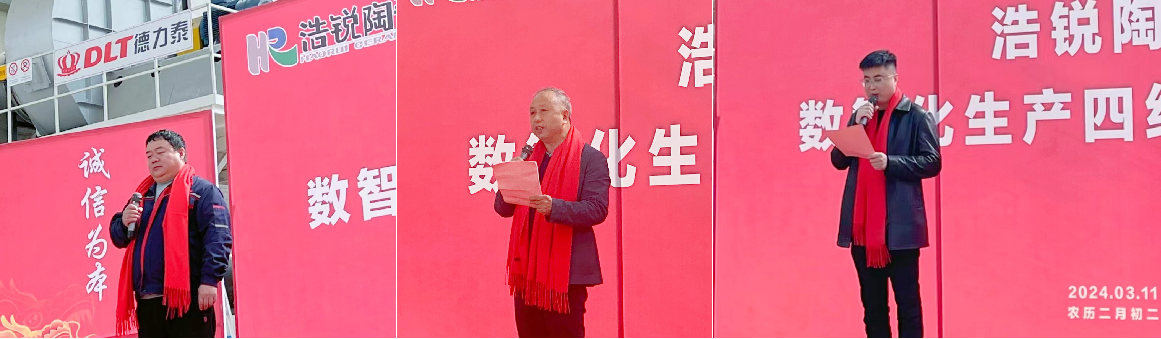
To meet the escalating demand for high-end consumption in the local area, this project is positioned to offer Hebei's superior quality, lowest energy consumption, and the most advanced levels of automation and digitization in production lines.
The project introduces machinery from HLT&DLT, including a set of HLT Technology PST45000 ultra-large energy-saving and environmentally friendly spray towers capable of producing over 2,000 tons of powder per day, 4 upgraded and revamped high-quality models YP5009 automatic hydraulic presses from HLT Industry, as well as the "4.0 Energy Efficiency Benchmark Smart Era" DGF firing kiln and DHD-EM6 series six-layer dryers and glaze line dryers from DLT.
The primary production specifications include high-end full polished glazed products of 400×800×7.5mm and 750×1500×10.5mm, with a daily production capacity of 25,000㎡.
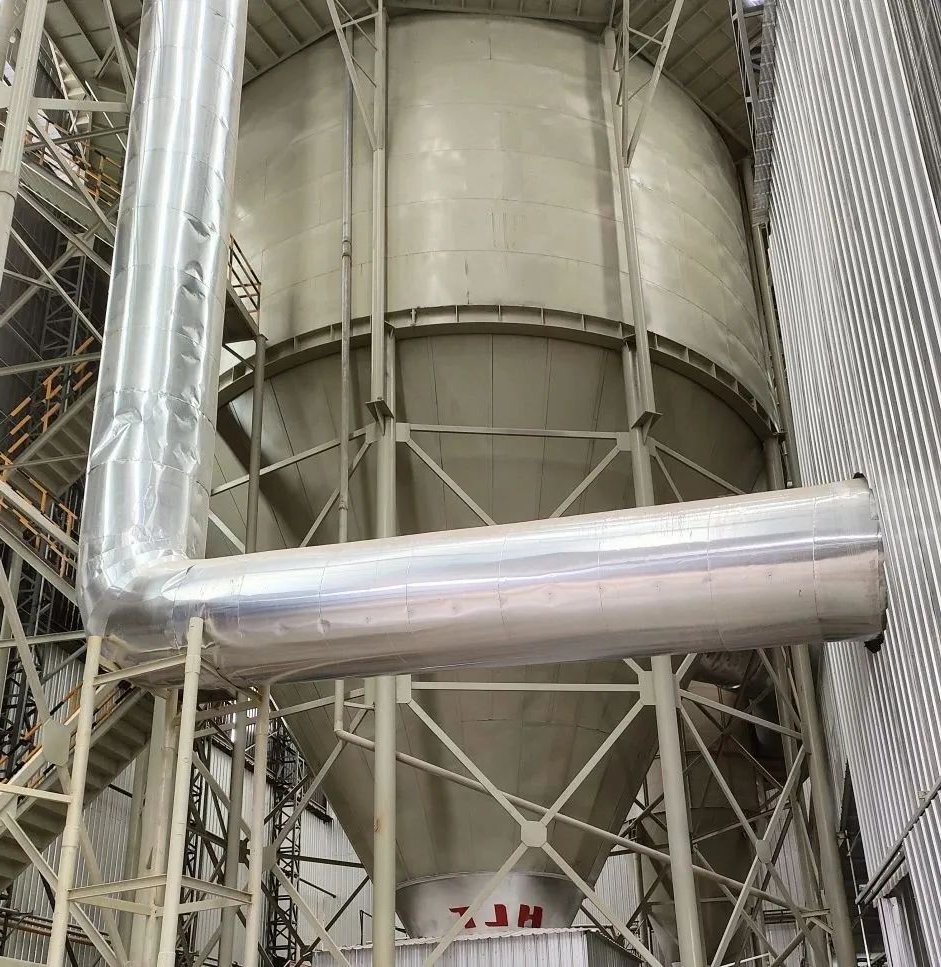
▲PST45000 energy-saving and environmentally friendly spray tower
The PST45000 energy-saving and environmentally friendly spray tower, newly introduced by HLT Technology, embodies a blend of energy efficiency, environmental friendliness, intelligence, and high production capacity and space-saving attributes, with a daily output production capacity of up to 2,500 tons.
Advantages:
- Evaporation energy consumption is no more than 750 kcal/kg of water, compared to traditional spray towers with energy consumption not lower than 800 kcal/kg of water.
- Equipped with advanced self-control systems including automatic slurry supply, automatic regulation, automatic tapping, and computerized control, this spray tower maximizes the automation of the pulverizing process, thereby reducing the need for manual intervention and easing the workload on operators.
- It achieves a production capacity equivalent to more than 3 sets of traditional machinery, saving more than 10 workers in operation and over half of the workshop space, while reducing tail powder emissions by 40%, thereby minimizing environmental pressure.
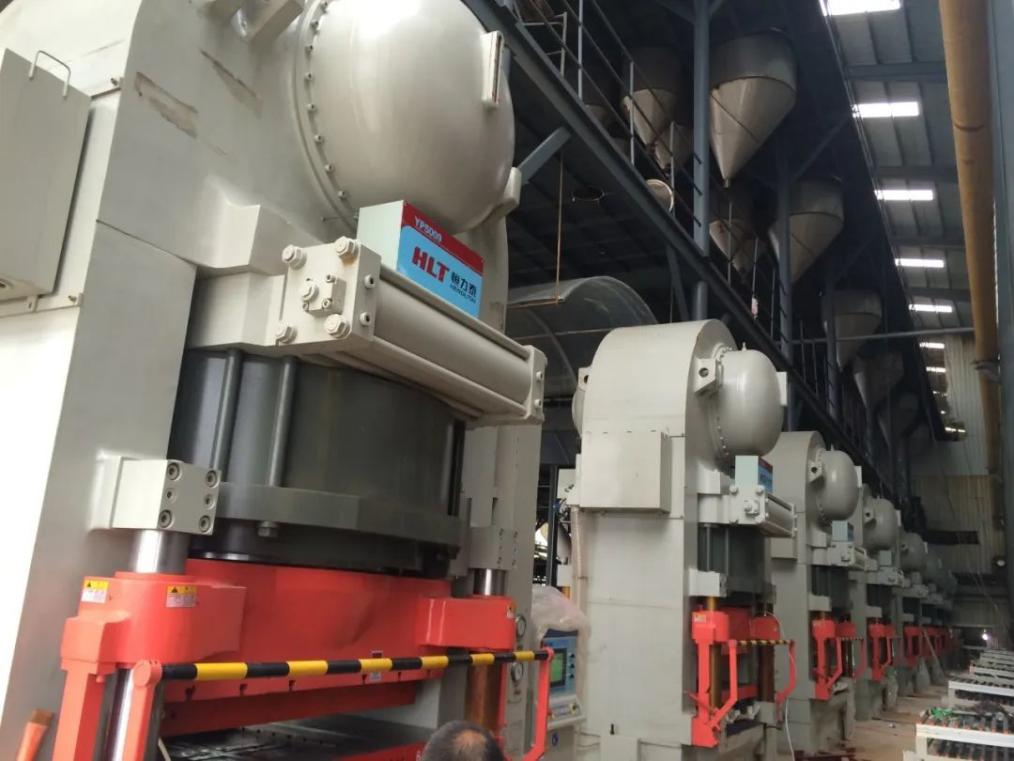
▲YP5009 Automatic Hydraulic Press
The HLT YP5009 Automatic Hydraulic Press represents a brand-new upgraded and revamped model, boasting multiple patented technologies. It enjoys widespread popularity in both China and international markets and is capable of producing a variety of tile specifications, including 600x600mm, 600 x 1200mm, 800 x 800mm, and 800 x 1200mm.
Advantages:
- The main unit adopts a prestressed wire-wound structural frame optimized for girder structure, ensuring exceptional fatigue resistance and stability under load.
- The Innovative design of the main cylinder structure introduces a novel external piston dynamic structure, enhancing the reliability and productivity of the brick press.
- Through scientific optimization and technological advancements, the forming quality of large-format ceramic tile blanks is ensured.
- The improved constant-pressure variable pump, combined with a high-volume accumulator oil supply system, speed and pressure boosting system, closed-loop control of moving beam position, and closed-loop control of main cylinder pressure, brings significant improvements in pressing speed, repeatability of actions, and energy efficiency. These enhancements effectively elevate the comprehensive performance of the machine
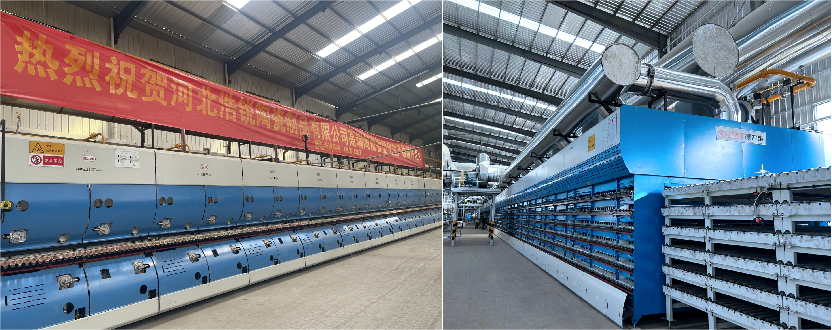
▲"Energy Efficiency Benchmark Smart Era" Firing Kiln
To better align with its brand image and green development philosophy, this firing kiln utilizes the advanced DDI4.0-A digital intelligent control system developed by DLT, as well as patented technologies such as the DHR efficient relay recovery cooling waste heat system and the PPC precise combustion assistance control system.
These systems enable precise proportional combustion, with smoke directly utilized in the six-layer drying process, achieving a 60% heat recovery from smoke and an overall energy saving of 25%. This achieves the goal of even lower carbon emissions and more energy-efficient operations.
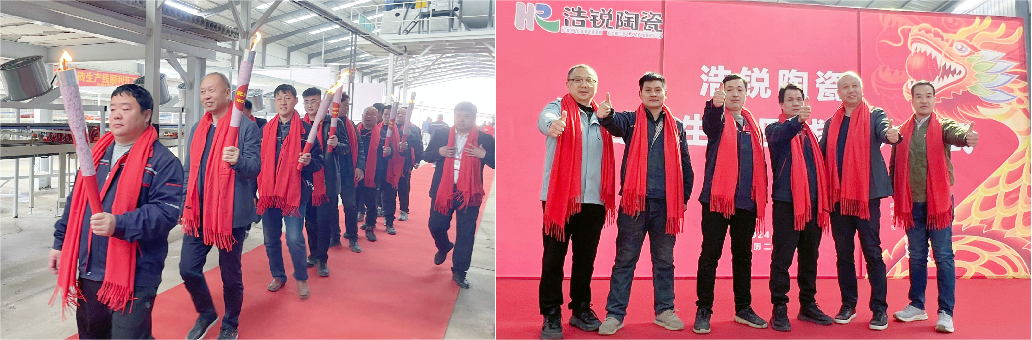
The EM series high-efficiency and energy-saving self-circulating six-layer dryer adopts a low-temperature rapid convection drying system, offering advantages such as minimal temperature difference, excellent stability, reduced mechanical cracking, strong regularity of tile blanks, high drying efficiency, and high automation level.
Additionally, the strength of the dried products is 10-15% higher compared to conventional dryers, making it the preferred weapon for numerous building ceramic manufacturers.
(HLT&DLT)