What does a "smart" factory look like?
Recently, stepping into Foshan KEDA Equipment Manufacturing Co., Ltd. (referred to as "KEDA Equipment"), the production line is brimming with "black technology". Each stage from material storage, welding, annealing, and processing, to coating operates efficiently under the command of the "smart brain".
Recently, stepping into Foshan KEDA Equipment Manufacturing Co., Ltd. (referred to as "KEDA Equipment"), the production line is brimming with "black technology". Each stage from material storage, welding, annealing, and processing, to coating operates efficiently under the command of the "smart brain".
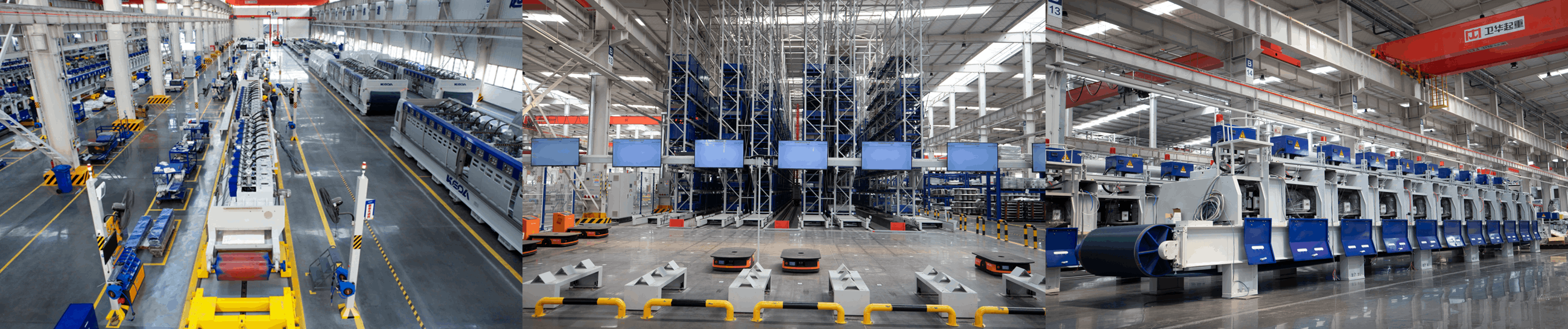
Located in Lubao Town, Sanshui District, KEDA Equipment is a wholly-owned subsidiary of KEDA Industrial Group Co., Ltd., a leading enterprise in Foshan. At the end of 2022, the company invested in and constructed the Machinery Intelligent Manufacturing Base project in Lubao High-end Machinery Manufacturing Industrial Park, officially commencing production in April this year.
As a typical discrete machinery manufacturing industry, KEDA Equipment has overcome the challenge of non-standardization by designing and constructing an advanced "one stream" production line. It applies 5G + industrial Internet technology to create a green intelligent factory, providing a reference model for the large-scale machinery manufacturing industry.
Optimized Layout to Achieve " One Stream" Production
In the warehouse area of the production workshop, long mechanical arms "fly" in the air, completing the required actions to move 12-meter-long profiles into the stereoscopic warehouse. On a towering 9-story stereoscopic warehouse shelf with a total storage capacity of nearly a thousand tons, rows of profiles are neatly stacked, awaiting instructions to be issued. They proceed automatically through the next steps via automated devices, then move on to processes such as unloading, robot welding, sandblasting, painting, and other production stages. This was the scene witnessed by reporters on May 27th at the production workshop of KEDA Equipment Project Phase I. The complete production process flows smoothly, requiring only a few workers to operate machinery control consoles.
However, factories designed and customized for the complete process—from unloading, welding, annealing, and machining to bottom coat painting—in a "one stream" manner are rare among large machinery manufacturing enterprises. "The Phase I project of KEDA Equipment can be said to be a benchmark for the large machinery manufacturing industry to build a digitalized factory," said Mr. Guosheng ZHOU.
As a typical discrete machinery manufacturing industry, KEDA Equipment faces a key word in building a digitalized factory: non-standardization. The products manufactured by KEDA Equipment are mainly used in industries such as ceramic machinery and stone processing. These products are characterized by large specifications, heavy weight, and customization, making them unsuitable for standardized assembly line operations. As a result, they cannot be mass-produced or produced in large scale batches. To improve production efficiency, breakthroughs must be made in production line design. At the beginning of construction, Mr. Guosheng ZHOU visited over 100 similar machinery manufacturing enterprises across China to find solutions: "There are almost no reference samples available in China, so we can only cross the river by feeling the stones."
According to process requirements, KEDA Equipment has customized advanced CNC machining machinery, established intelligent three-dimensional warehousing, adopted heavy-duty AGVs, shuttle cars, and accumulation chains for intelligent material transport, and implemented a 5G network layout to achieve device interconnection. The machinery is equipped with data acquisition chips that can collect real-time data and implement partial algorithmic decisions. Thus, a "one stream" large-scale machinery production factory has been realized in KEDA Equipment Project Phase I.
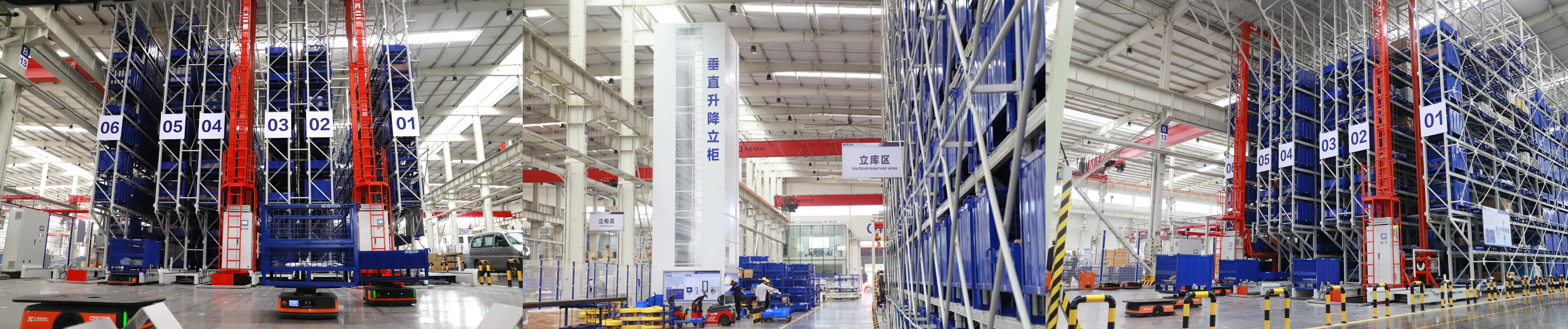
Mr. Guosheng ZHOU stated that KEDA's "one stream" production line layout is forward-looking, with a wide application of digital intelligent machinery and technology, ensuring that the factory operation stays ahead for 5 years and does not fall behind for 10 years. In his view, "one stream" not only saves time in each production process and improves efficiency but also lays the foundation for creating a digitalized factory.
Looking solely at KEDA Equipment's stereoscopic warehouse system, this function completely departs from traditional warehouse management, becoming an integral part of manufacturing.By integrating ERP, WMS, and WCS information systems, it achieves fully automated processes from sorting to loading and unloading, with precision reaching millimeters. The clever application of the intelligent stereoscopic warehouse at KEDA Equipment not only saves space and reduces labor costs in logistics but also enhances production efficiency and accuracy.
KEDA Equipment's construction of a digitalized factory is reflected not only in its advanced production line design but also in its utilization of technologies such as 5G + industrial Internet. Mr. Guosheng ZHOU mentioned that currently, all KEDA Equipment devices are embedded with IoT chip cards, achieving full 5G network coverage. This hardware essentially meets the requirements of a digitalized factory. With subsequent configuration and management through software applications, connecting to dynamic host servers to obtain machinery operation IPs, KEDA Equipment can realize the interconnection between people, machines, and materials. Based on data collection, processing, and analysis, it can implement algorithmic decision-making and provide powerful assistance for human decision-making.
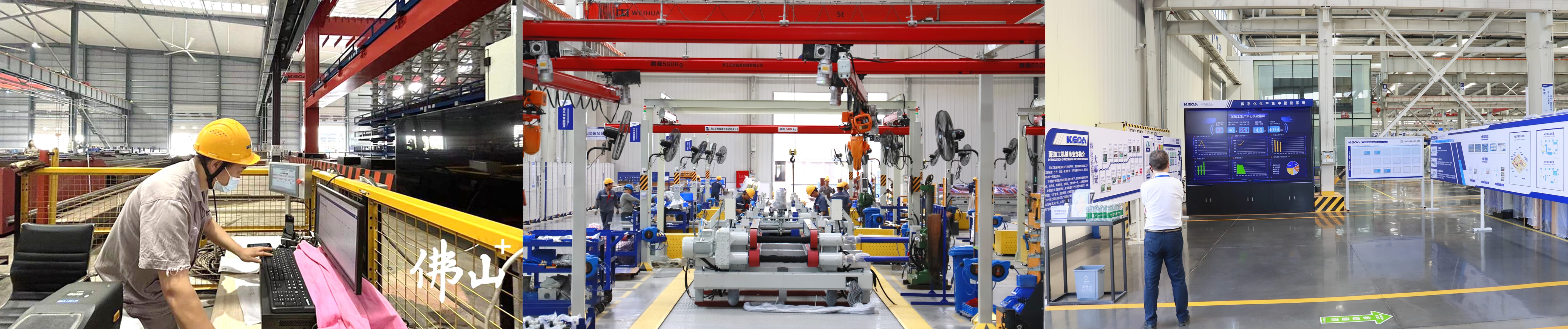
It was introduced that KEDA Equipment Project Phase I includes the construction of 7 buildings, of which 4 are production workshops. These include 7 welding lines, multiple machining production lines, and 3 painting lines, with an annual metal processing capacity reaching tens of thousands of tons. Significantly, the KEDA Equipment project also fully considers energy conservation and environmental protection requirements. Photovoltaic panels are installed on the roofs of the 7 buildings. After the grid connection, the annual electricity generation is expected to reach around 7 million kilowatt-hours. This will meet part of the project's electricity needs, achieving cost reduction and efficiency enhancement.
Although KEDA Equipment Project Phase I has recently commenced production, it has already provided partial large-scale processing parts supporting services to leading enterprises in the large stamping and injection molding industries in southern China, including listed companies. "We already have orders scheduled until August," Mr. Guosheng ZHOU stated that it is foreseeable that with the support of 5G and the industrial Internet, KEDA Equipment's pace of intelligent manufacturing will accelerate, undoubtedly injecting new momentum into the development of the machinery manufacturing industry in South China.
Although KEDA Equipment Project Phase I has recently commenced production, it has already provided partial large-scale processing parts supporting services to leading enterprises in the large stamping and injection molding industries in southern China, including listed companies. "We already have orders scheduled until August," Mr. Guosheng ZHOU stated that it is foreseeable that with the support of 5G and the industrial Internet, KEDA Equipment's pace of intelligent manufacturing will accelerate, undoubtedly injecting new momentum into the development of the machinery manufacturing industry in South China.
(Xiaojie Lu, Foshan News Media Center)