The outbreak of the COVID-19 pandemic in 2020 has to some extent facilitated the process of "Localization" for KEDA India. After the gradual repatriation of Chinese employees, KEDA India shifted its operations to a fully Indian workforce structure, with Chinese management personnel overseeing operations through video conferencing. As of now, KEDA India has nearly 50 Indian employees, with only 7 remaining Chinese staff members. Until now, the entire local workforce of KEDA Industrial Group in India has exceeded one hundred employees. Localized operations have become the primary choice.
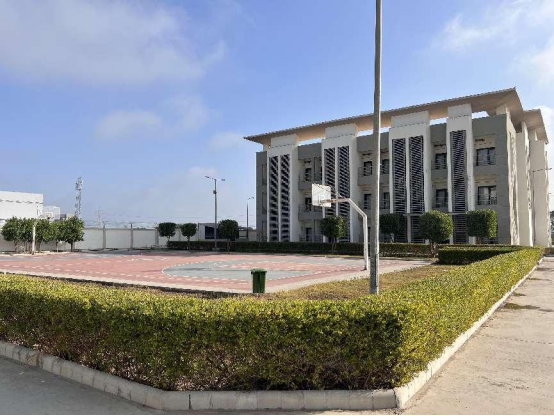
KEDA India's office building
Respect and Cultural Integration
India is a nation rich in religious beliefs. To earn the respect and trust of its employees, KEDA India recognizes that cultural integration is an essential path to follow. In 2022, after a three-year separation due to pandemic-induced isolation and the issuance of visas, KEDA India's General Manager, Pan HU, along with the General Manager of KEDA Ceramic Machinery's Indian sales division, Wei ZOU, and 5 other Chinese personnel, promptly returned to KEDA India.
When in Rome, do as the Romans do. Respecting the local religious beliefs is crucial for achieving better cultural integration. Upon their return to KEDA India, under the guidance of the Chinese management team, the company organized three large-scale local Indian celebrations. What made these events different from the past was the active participation of Chinese employees, who joined their Indian colleagues in the festivities. Through these large-scale local activities, both Chinese and Indian employees deepened their understanding of each other, and the company gained momentum through the continuous blending of cultures". With their culture as the basis for communication, we subtly infused some of KEDA 's concepts during the ceremonial activities, creating a harmonious atmosphere and bringing us closer," remarked Pan HU.
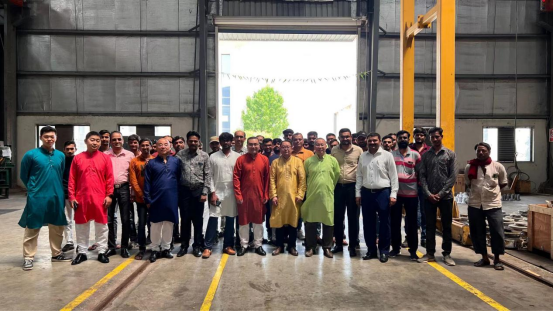
Chinese and Indian employees dressed in traditional Indian attire, Kurta, pose for a photo
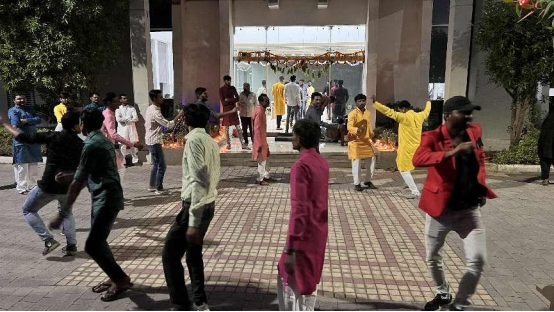
Staff singing and dancing at the fellowship activity
The core of cultural integration lies in inclusiveness and respect. Last year, KEDA India hired a Nepalese chef to provide authentic Indian cuisine for its local staff, fostering a stronger sense of camaraderie among Indian staff. Mutual respect allows us to enter each other's inner worlds. Recognizing the importance of family to Indians, the Chinese management team visited the homes of various employees, sharing meals and engaging in conversations about their families, beliefs, and topics of interest. By opening their hearts, they facilitated better communication, which in turn fostered a more conducive work environment for the future.
Nurturing a Fertile Ground for Talent, Opening Pathways to Success
As early as 2021, in order to facilitate on-site management and unlock the potential of localized human resources, KEDA India gradually appointed Indian managers in various departments, establishing an organizational structure with one Chinese manager and one Indian manager per department. This initiative has created a clear career advancement path for Indian employees and greatly stimulated the enthusiasm of grassroots Indian managers.
The utilization and reappointment of local managers is a vital measure implemented by KEDA India, tailored to the local circumstances. Nikunj M, the Deputy Manager of the Production Department, was previously an ordinary belt splicer in KEDA India's production department before the COVID-19 pandemic. It was his sense of responsibility and dedication demonstrated during the pandemic that led to his unwavering commitment to working overtime and conducting belt splicing at customer sites despite the challenges. In recognition of his exceptional performance, he was swiftly promoted to a supervisory role. In recognition of his exceptional performance, he was swiftly promoted to a supervisory role. In his personal reflection as the recipient of the Outstanding Employee Award for 2021, Nikunj M wrote, "In the past year, I have given my all to the company, and in the future, I will continue to dedicate myself to KEDA with even greater efforts. I am fortunate to work at KEDA India!" His genuine passion fuels his unwavering dedication to his work, and his outstanding performance and potential for growth have earned him the promotion to Deputy Manager of the Production Department.
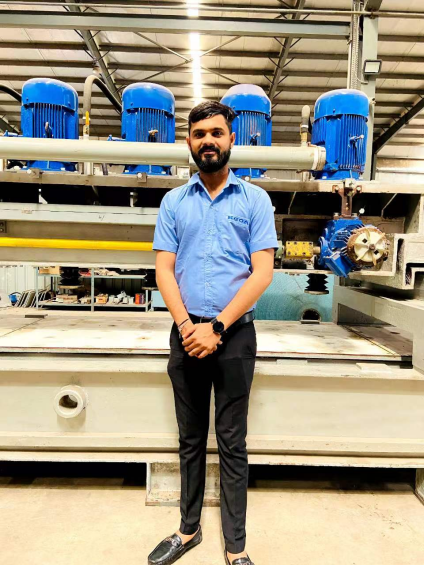
Nikunj.M, the Deputy Manager of the Production Department
Manoj, who has a professional background with German and Italian companies, currently holds the position of Finance Manager (Indian manager) at KEDA India. He joined KEDA India in 2016, during the early stages of the company's establishment. At that time, with the financial system and framework being virtually non-existent, Manoj led a team of two other Indian employees to delve into the frontline, gaining a deep understanding of the unique aspects of each business in the local Indian context. This allowed them to streamline and draft operational processes and management systems for each business sector. After formulating these processes, Manoj actively and effectively communicated and coordinated with other departments, constantly identifying and addressing loopholes and deficiencies in the systems and processes. Through the efforts of Manoj and his team, KEDA India's financial management framework, all business processes, and operational management internal control systems were built from scratch and gradually established. Manoj himself stated, " KEDA India is an important milestone in my career, providing me with ample room for personal growth. Here, I can freely express my thoughts, and my superiors listen attentively and selectively adopt my suggestions." Undoubtedly, the Finance Department of KEDA India, as a pioneer in the localization of financial management within KEDA Industrial Group's overseas operations, has taken the first step in establishing a mature financial management system for overseas subsidiaries, providing valuable experience and a foundation for future overseas subsidiaries. Manoj's contributions are instrumental in this endeavor, serving as a prime example of a localized management talent finding a perfect fit.
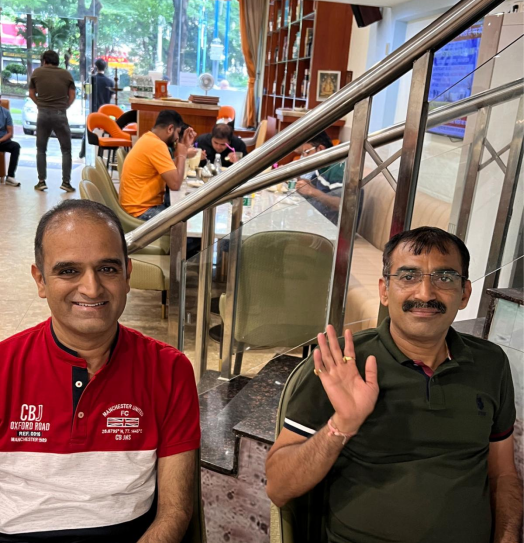
Manoj, the Finance Manager of KEDA India (left), and Rajesh, the Assistant General Manager (right)
Establishing a management system to unearth management benefits
Due to cultural differences, Indians generally have a casual and free-spirited approach, especially in the case of KEDA India where Chinese management personnel were unable to be present on-site for an extended period due to the special circumstances of the pandemic. It became imperative to establish a localized management system.
During the global impact of the COVID-19 pandemic, KEDA India accelerated the development of its internal processes. Based on the subsidiary's specific situation, KEDA India established its own OA platform and optimized the SAP system. Additionally, due to the restriction on WeChat usage in India, KEDA India chose to use DingTalk as the software for daily office communication. Through secondary development, functionalities such as personnel attendance, sales order processing, and delivery were implemented. These measures have to some extent contributed to KEDA India's journey towards "process management”.
In day-to-day management, the KEDA India management team believes that "there is no right or wrong in management; adapting to local conditions is the most appropriate approach." During the pandemic, KEDA India combined the characteristics of the local Indian office environment and formulated a meeting management system. The system includes a weekly management meeting that is scheduled at 9:00 a.m. Indian time and 11:30 a.m. Chinese time, where management personnel from both China and India hold video conferences to discuss the week's events. Furthermore, considering the rapidly changing nature of the Indian market, all sales personnel are required to hold online sales meetings at scheduled times each day, enabling them to stay up-to-date with market dynamics and adjust sales strategies promptly. The institutionalization and implementation of such meeting management systems effectively facilitate information dissemination, strengthen mutual trust, and provide important references for Chinese management personnel in formulating and adjusting relevant strategies in the future.
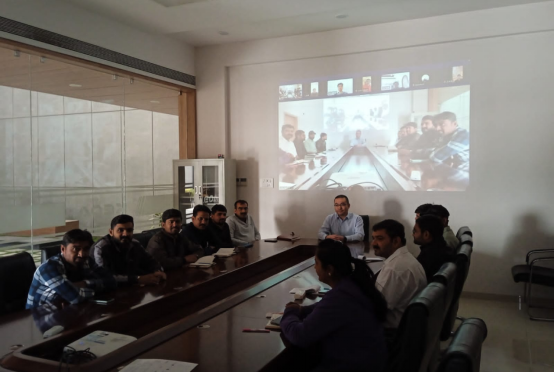
Chinese and Indian employees hold video conferences
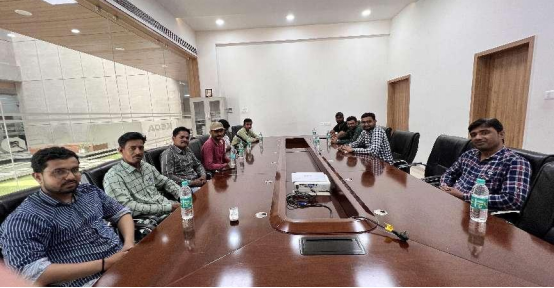
Indian employees participating in the weekly management morning meeting
In the latter half of last year, in order to enhance the sense of belonging among Indian employees, the Chinese management team devised an "I Love My Home" all-staff cleaning activity. Initially, the participation was not very enthusiastic. Pan HU led by example, personally wielding a broom to clean the entrance. The activity emphasized that "cleaning is not just for the company, but for our home". Consequently, everyone picked up their tools and joined in the cleaning effort, completing the originally planned half-day activity in just two hours. Through this activity, the office and factory environment of KEDA India were revitalized, presenting a better image for welcoming guests and business partners, and Indian employees also strengthened their sense of ownership during the event.
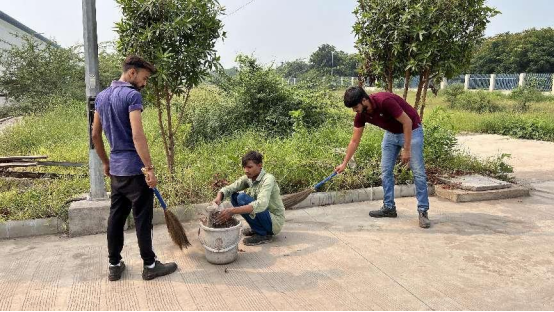
The scene of the "I Love My Home" all-staff cleaning activity
To achieve higher management efficiency through localized operations, KEDA India selected and recommended an Indian assistant general manager named Rajesh. "Due to cultural differences, it takes a lot of effort and time to get employees to accept instructions if they are delivered in a Chinese manner. However, with an Indian assistant, often a single sentence from him is enough to get things done. On the other hand, I also emphasize to Chinese management personnel that when communicating and collaborating with foreign employees, we must avoid rigid thinking, assuming that our own ideas and actions are always right. We must engage in open-minded exchanges with them," said Pan HU. However, he is continuously exploring the depth of localized management. "Managing solely based on Chinese culture is certainly not viable, but managing solely based on Indian culture is also unreliable, as it may bring in the management pitfalls existing in Indian companies. It is best to combine the cultures of both sides to form a comprehensive approach, integrating KEDA 's corporate culture. Only such management will possess adaptability and long-term sustainability. I am also working on aligning with the assistant general manager, seeking common ground while respecting differences, in order to enhance the company's management efficiency and yield real management benefits."
The journey toward "localization" is still a daunting task...
Localization is a complex issue that encompasses a wide range of areas. In addition to the aforementioned localization efforts, KEDA India is also accelerating the localization of its production and manufacturing. Prior to the COVID-19 pandemic, KEDA India primarily relied on Chinese technicians to handle the refurbishment projects for polishing machine assemblies, with Indian employees providing minimal assistance. However, when the pandemic struck and all Chinese employees returned to their home country, the refurbishment projects came to a halt due to a lack of technical support. Towards the end of last year, the Chinese management team recognized the potential of localized production and manufacturing in India. However, they still had concerns about the absence of Chinese technicians. It was at this critical juncture that Nikunj.M stepped forward and volunteered to lead a team in an attempt to refurbish the polishing machine assemblies. Many people were skeptical at the time and believed that it would be impossible to carry out the refurbishment without Chinese technicians. However, with great determination, Nikunj.M and the team managed to successfully complete the product, earning the admiration of all. This achievement of refurbishing the polishing machine assembly solely with the efforts of Indian employees opened up new possibilities for localized production and manufacturing. Additionally, KEDA India has also established upstream channels for local production and processing, as well as certain local sourcing and procurement resources.
In the process of overseas localization, aside from actively nurturing and utilizing local employees, the collective contribution of Chinese employees is also indispensable. During the three years when the Chinese employees of KEDA India were unable to be physically present at the site, they made every effort to ensure work coordination and communication, dedicating tremendous efforts behind the scenes. Due to the 2.5-hour time difference between China and India, Chinese employees maintained working hours of more than ten hours each day to maximize overlapping working time with the Indian site and clients. Working until 8 p.m. became a routine. The monthly online video inventory check, conducted for the sake of material safety, proved to be the most time-consuming and labor-intensive task. Overcoming the barriers of time and communication, they meticulously conducted inventory checks via video, ensuring the accuracy of the company's inventory data.
With the support of localization, KEDA India will continue to move forward pragmatically, embracing continuous transformation and innovation, and undoubtedly embracing a promising future!
(Jiasheng XIE, President Office)