From April 18 to 22, the 2025 Foshan Uniceramics Expo will be held at the Foshan Tanzhou International Convention and Exhibition Center. For this edition, KEDA Industrial Group will debut a "Exhibition + Manufacturing Base" dual-showcase model, with major exhibition machinery displayed directly at its production bases.
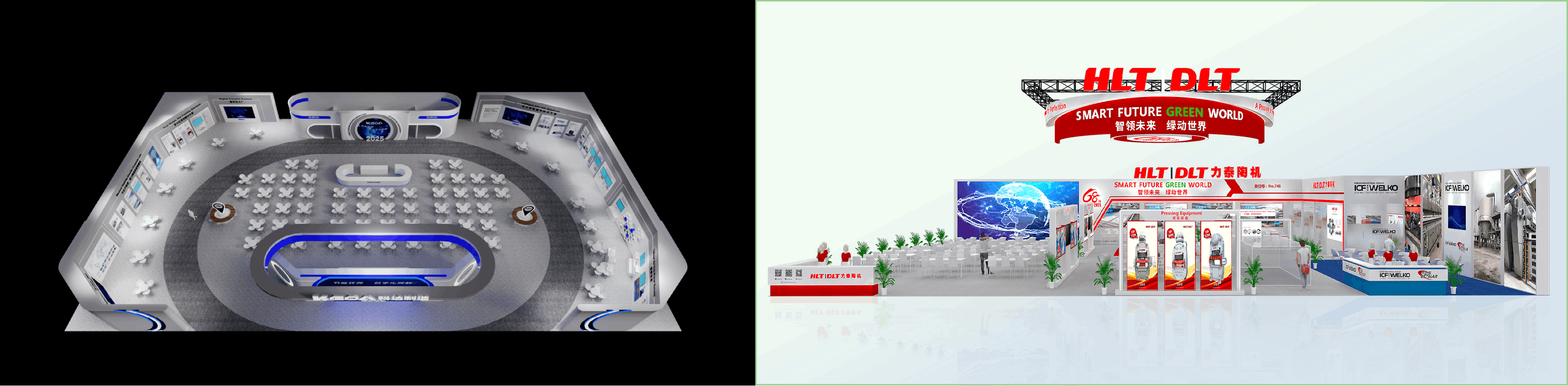
9 Major Manufacturing Bases Fully Open – Creating a Year-Round "Innovation Exhibition" that Never Closes
KEDA Ceramic Machinery and HLT&DLT have completed technical upgrades across all key product workshops and supporting facilities, welcoming global visitors with a refreshed & modernized manufacturing landscape.
At this exhibition, KEDA Ceramic Machinery will showcase the latest innovations and breakthroughs in intelligent ceramic production line machinery through a coordinated approach integrating "Technology + Product + Service".
Additionally, KEDA enables direct experience of its significant advancements in production and R&D by offering global customers on-site visits to its manufacturing bases. These visits highlight KEDA's integrated capabilities across the entire industry chain—from raw material machinery to after-kiln production lines, and from core spare parts to spare parts & consumables.
KEDA Ceramic Machinery has established a comprehensive "Intelligent Manufacturing Matrix" covering the entire ceramic production process, based on its 6 major manufacturing bases: Lunjiao, Guanglong, Dadu, and Xianchong plants in Shunde District, Foshan; the KEDA Machinery Manufacturing Base in Sanshui District, Foshan; and the KEDA Intelligent Manufacturing Base in the Zhenjiang Industrial Transfer Park, Shaoguan.
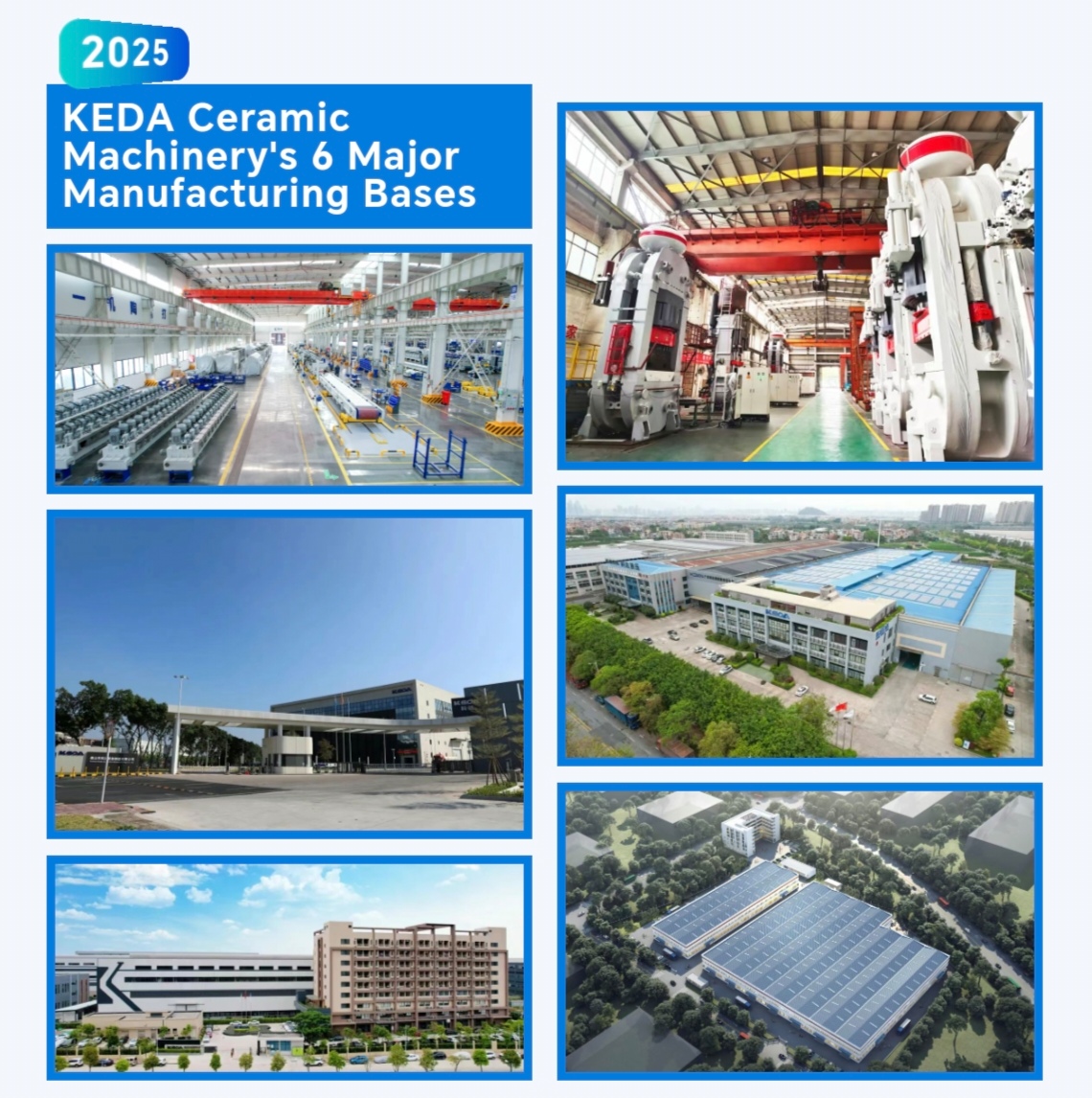
Supported by its 3 manufacturing bases in Sanshui District, HLT&DLT focuses on the R&D and manufacturing of complete production lines for ceramic raw material machines, presses, firing machines, and aluminum extrusion machines, driving industry transformation and upgrading with superior quality.
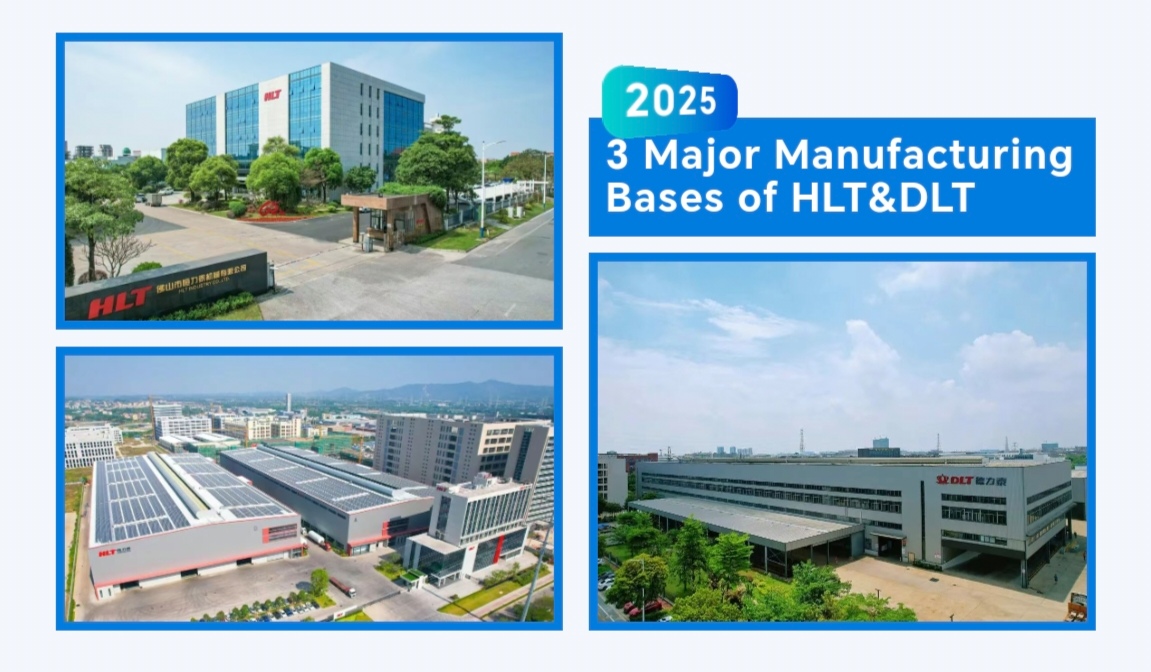
On the afternoon of April 18, KEDA Ceramic Machinery will host a new product and technology exchange event at the headquarters, featuring a centralized display of innovative products and technical sharing.
KEDA Ceramic Machinery: Global Reach, Digital Touch
▶ Third-generation Extenller-Slab Forming System
▶ Third-generation Extenller-Slab Forming System
Following three generations of technological upgrades, the third-generation extenller-slab forming system further enhances press speed & automation. Featuring high flexibility, it enables continuous production of ceramic large slabs, sintered slabs, and thin slabs with finished widths ranging from 800 to 1800mm and thicknesses from 3 to 20mm. The system is available in 1.2m, 1.6m, and 1.8m widths to meet the production needs of full-size sintered slabs.
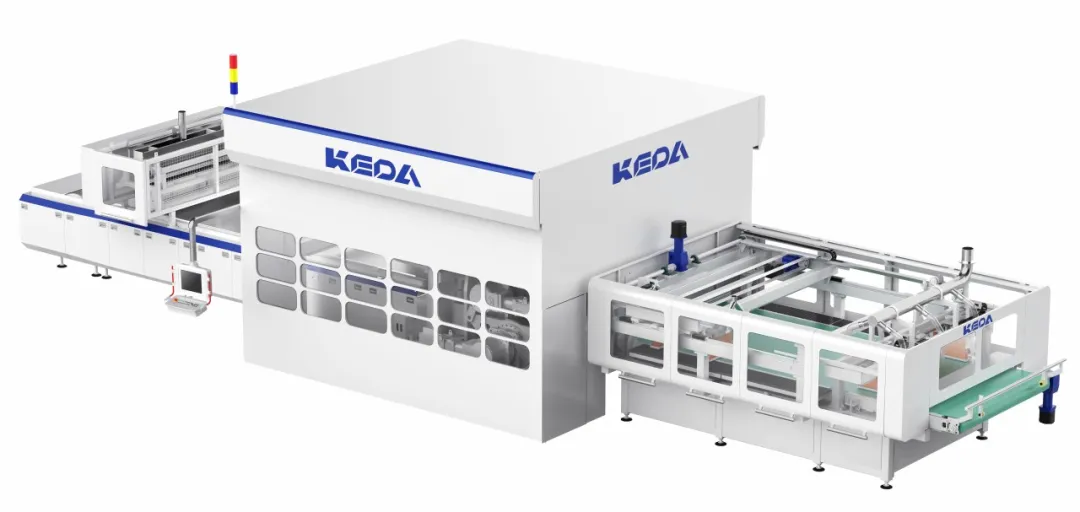
▶ AI-Driven Intelligent Ceramic Complete Production Line
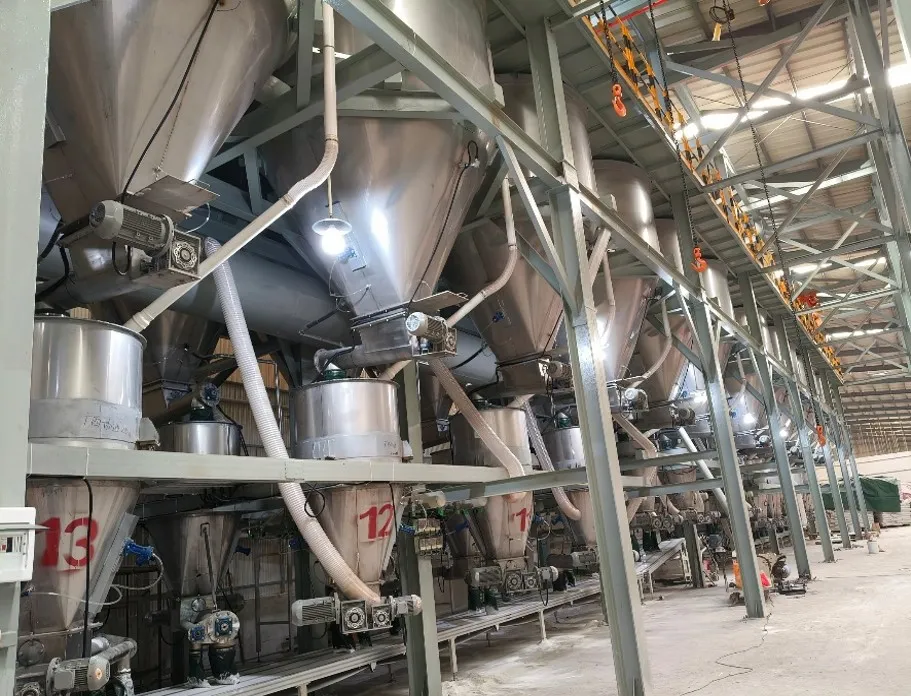
The system offers precise formula control, full automation, and a control accuracy deviation of ≤2%, significantly improving the working environment in glaze dosing workshops and achieving intelligent, automated glaze formulation to enhance product quality.
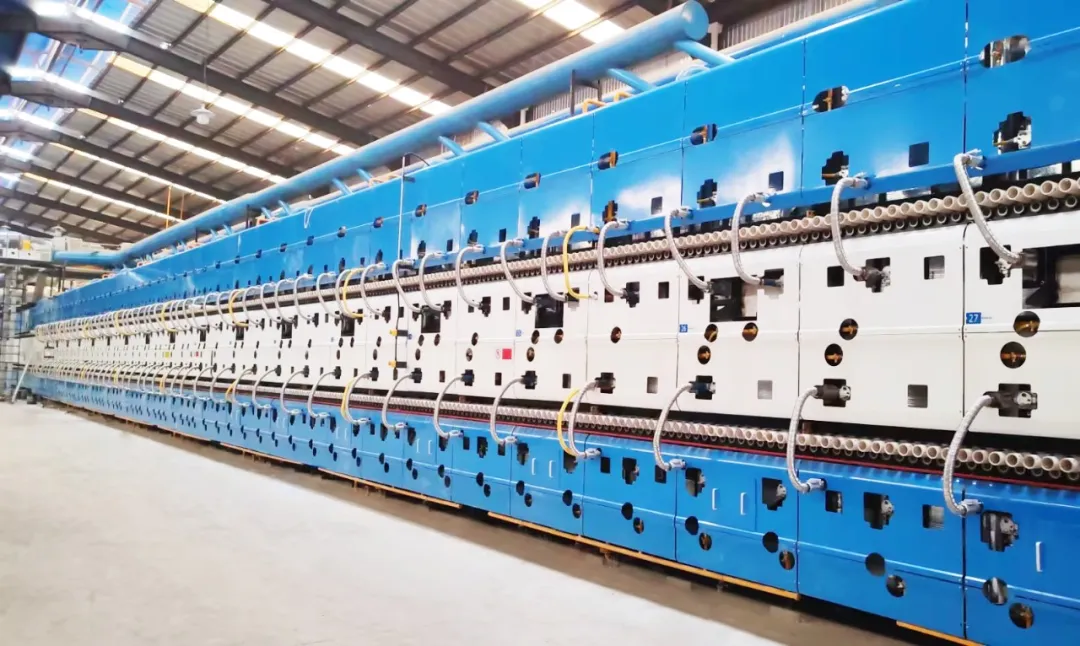
▶ Live Demonstration of Multiple Innovative After-Kiln Complete Production Line Products
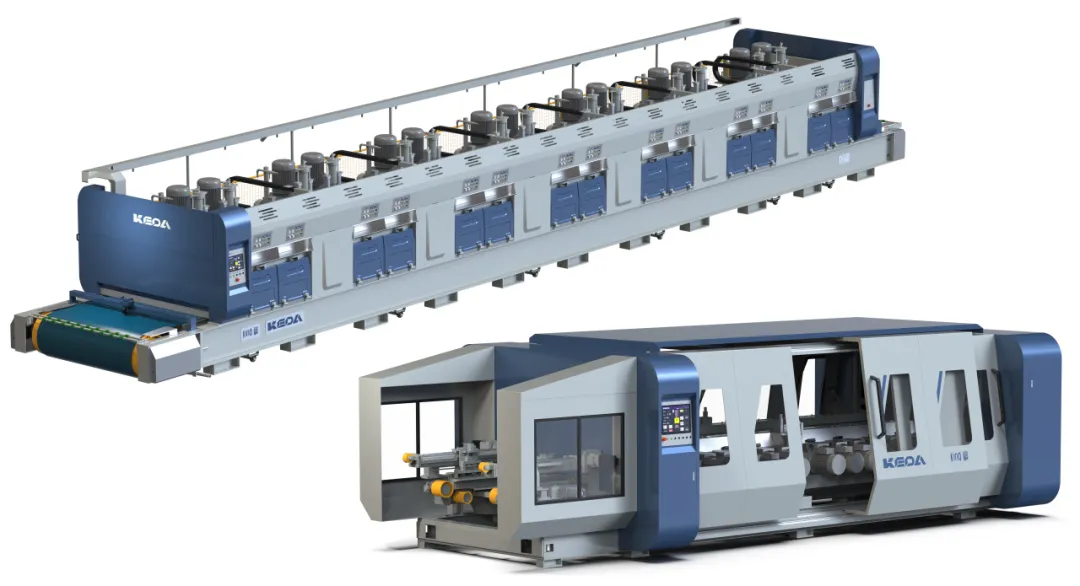
KEDA Logistics Machinery Division focuses on achieving intelligent & flexible production throughout the entire ceramic manufacturing process, from green bodies to finished products. This year's highlights include various combinations of AGV applications, such as the AGV + BOX pre-kiln compensator system and the AGV + sponge suction cup loading/unloading machine after-kiln storage system. Customized storage and logistics solutions are provided based on different site conditions.
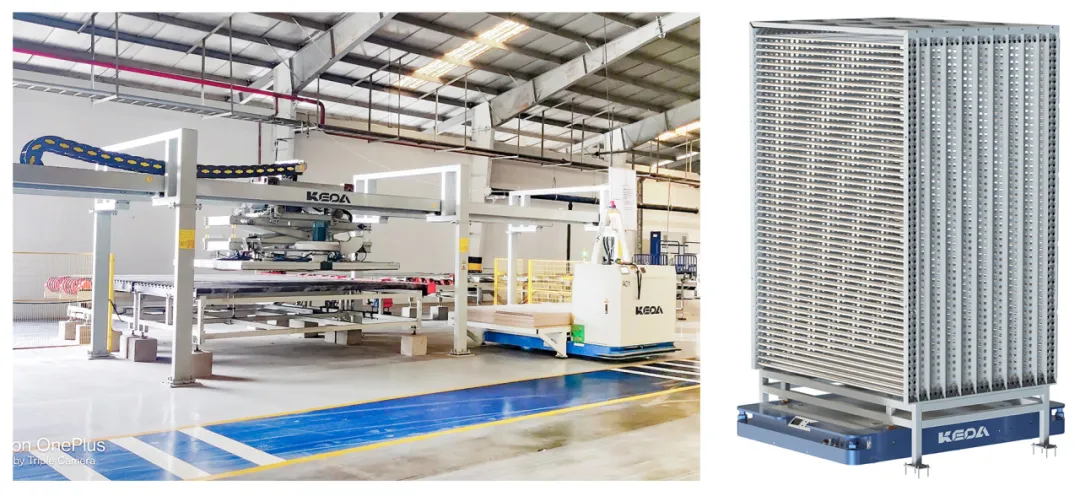
KEDA Sorting & Packaging Machinery Division introduces the newly designed KEDA KING Series rapid production transfer packaging machine, capable of achieving a packaging speed of up to 15.8 packs/minute (400×800mm). Featuring multiple patented technologies from KEDA, the machine offers multi-level parameter displays, efficient edge computing, and seamless integration with the KEDA OS system. It delivers stronger functionality and more intelligent, user-friendly operation.
▶ Diverse Services Creating Multi-Dimensional Value for Customers
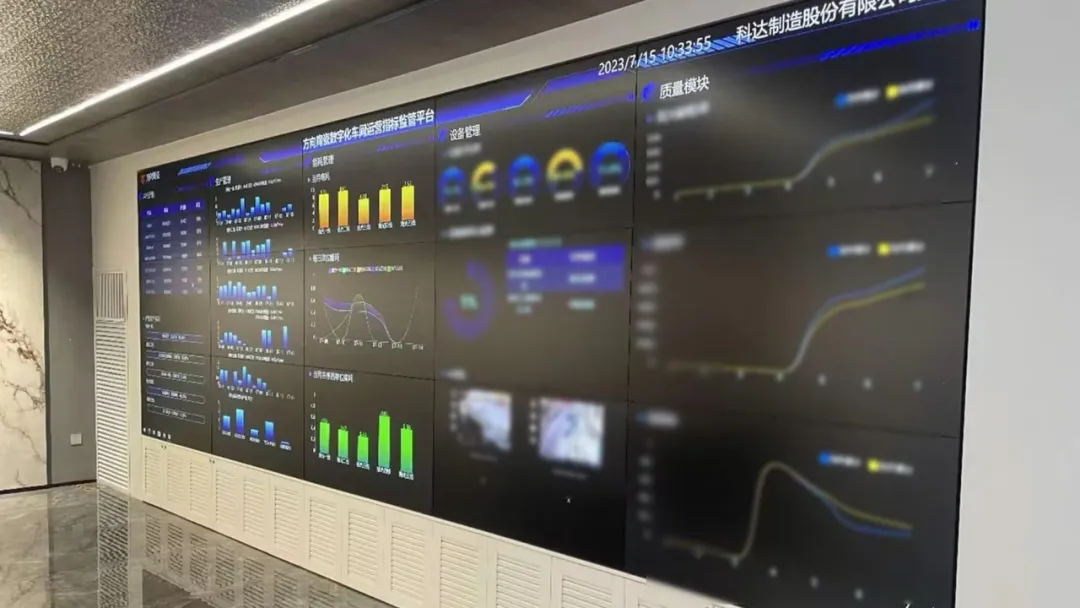
The KEDA Digital Factory System (CeramiX IMCS, formerly known as Zhentao MOM) includes 8 core functional modules covering production data acquisition, machinery operation parameter monitoring, machinery status monitoring, fault warnings, and more. It also integrates AI-assisted process quality decision-making functions, effectively reducing labor and management costs, improving operational efficiency, and accelerating the digital transformation of production management. The system provides an optimal solution for intelligent manufacturing upgrades in the ceramic industry.
▶ Launch of Energy-Saving, Environmentally Friendly, and Highly Efficient Raw Material Machines
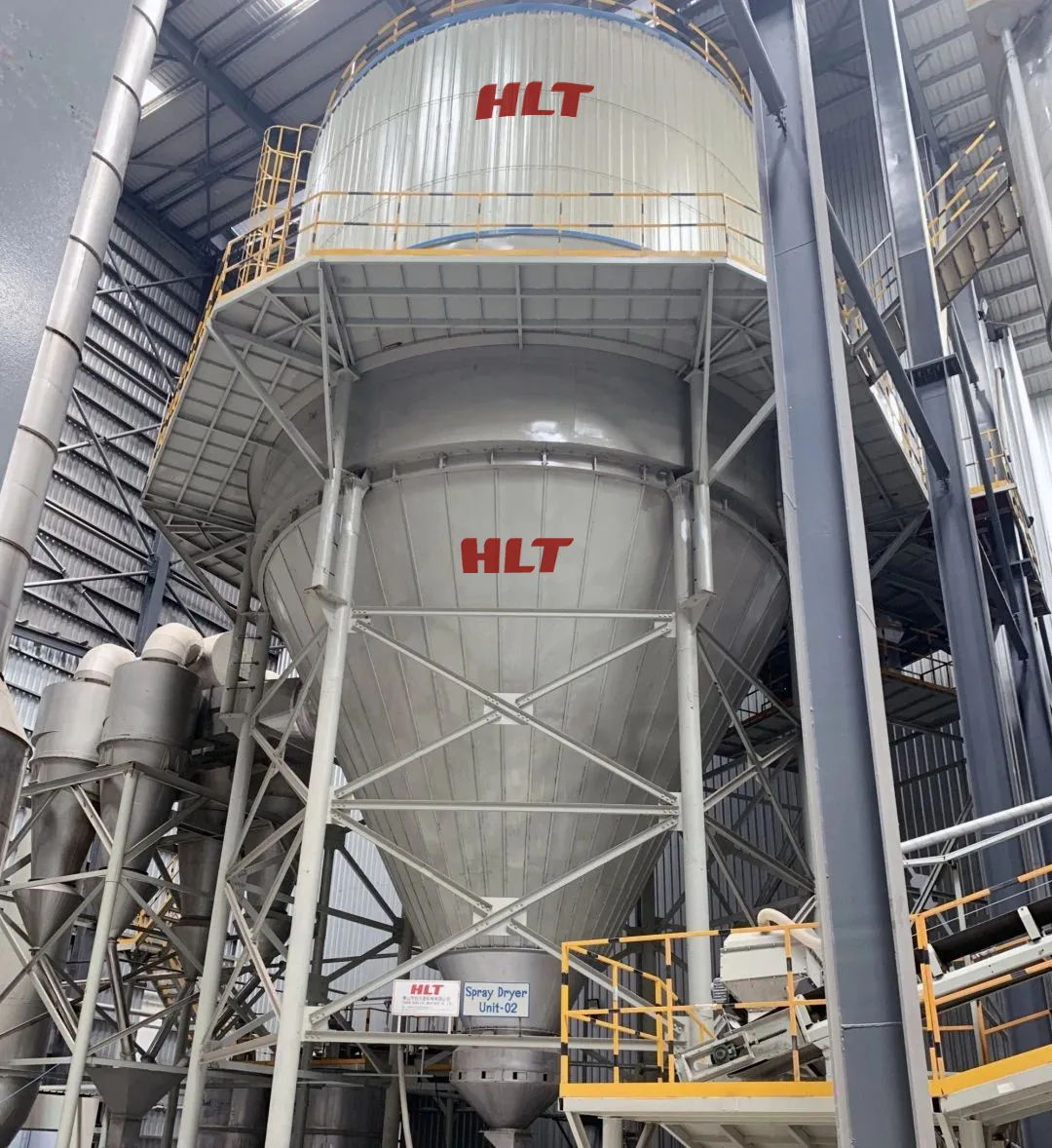
The digital, energy-saving continuous ball milling system includes multiple management modules such as automatic batching and feeding, machinery monitoring, energy consumption analysis, production reporting, and mobile app data monitoring. The system is user-friendly and easy to operate, with one-click startup functionality.
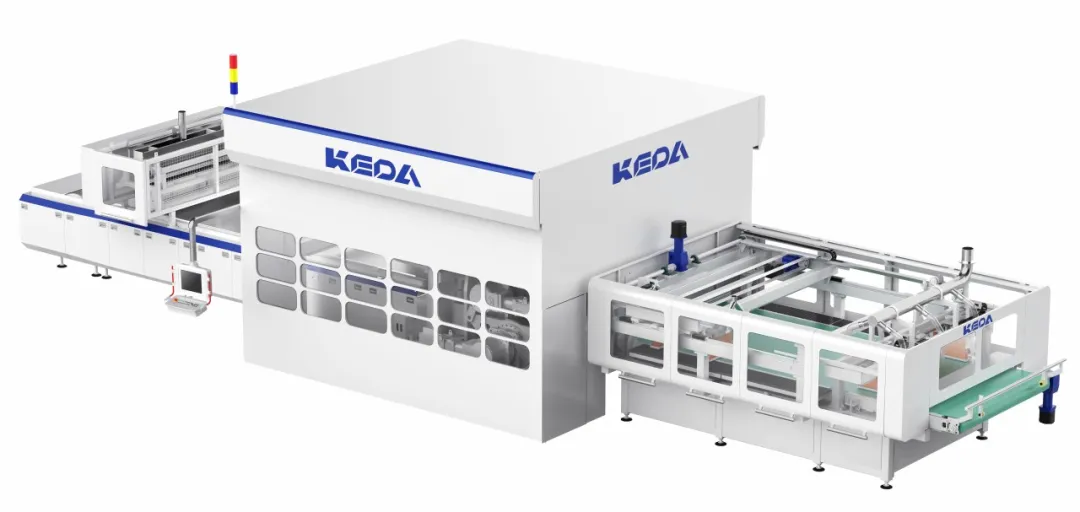
▶ AI-Driven Intelligent Ceramic Complete Production Line
Foshan KEDA Industrial Co., Ltd. takes the lead in integrating AI technology into kiln control systems, which capable of logical reasoning and analysis based on specific production requirements and product characteristics. The system provides advanced kiln process solutions, delivering customized & optimized firing strategies.
At the Lunjiao manufacturing base, Foshan KEDA Industrial will showcase a high-capacity spray dryer with a maximum daily powder output of 2,500 tons, and a continuous ball mill. It will also highlight a new-generation automatic glaze dosing system with an annual output of up to 120,000 tons of intelligent glaze material.
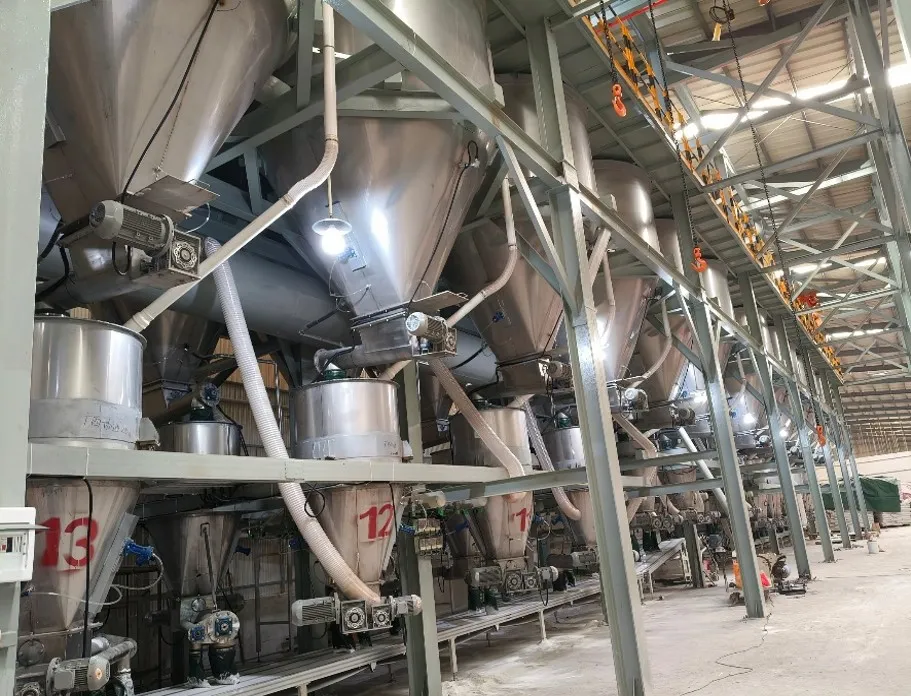
The system offers precise formula control, full automation, and a control accuracy deviation of ≤2%, significantly improving the working environment in glaze dosing workshops and achieving intelligent, automated glaze formulation to enhance product quality.
KEDA Ceramic Machinery's hydrogen-powered energy-saving wide kilns, 5G intelligent double-layer kilns, 6th-generation cecullar ceramics roller kiln production lines, zero-carbon combustion technology, as well as sanitaryware & tableware tunnel kilns, will be showcased alongside after-kiln production line machines in Workshop C11 at the KEDA Industrial Group Headquarters (Guanglong Base).
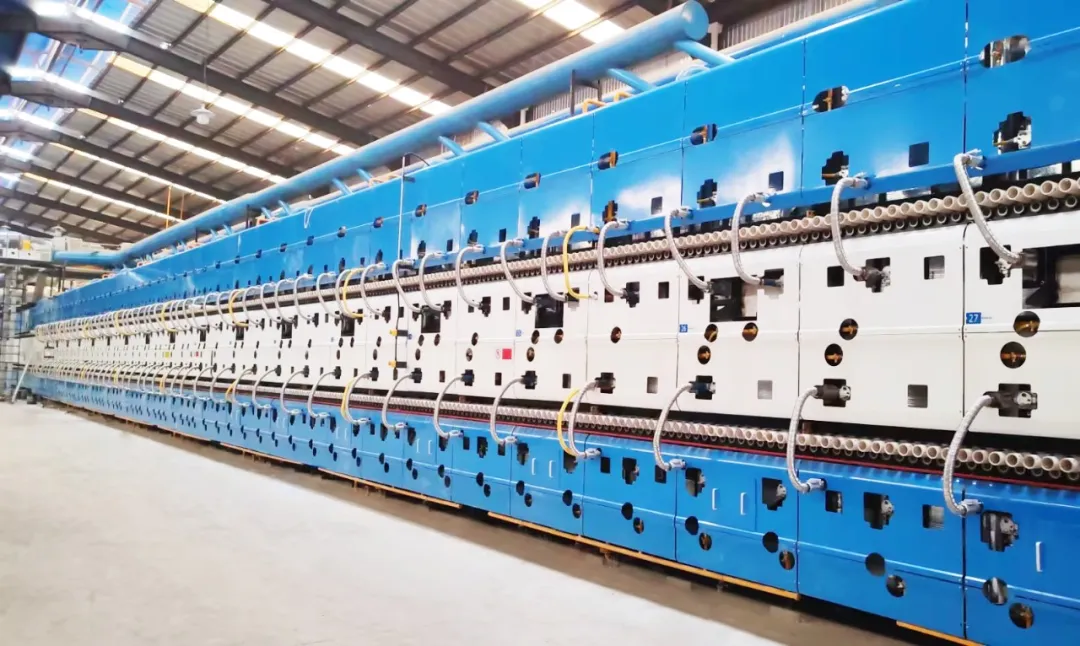
▶ Live Demonstration of Multiple Innovative After-Kiln Complete Production Line Products
KEDA's integrated planning of the after-kiln complete production line provides customers with the most economical & scientifically optimized total solutions. This significantly enhances production continuity & stability, improves the rate of high-grade products, and reduces overall operational costs—an achievement made possible by continuous innovation across KEDA's after-kiln complete product lines.
At this year's exhibition, KEDA Final Processing Division will present the full range of the new "KEDA KING Series", including the newly designed Second-generation KEDA KING series NC squaring & chamfering machine, KEDA KING series intelligent double-head swing polishing machine, and KEDA KING series intelligent single-head swing LUXCO coating machine. These machines help ceramic enterprises enhance surface flatness and gloss uniformity of tiles, enabling tight-joint paving, increasing production efficiency, and simplifying the production process.
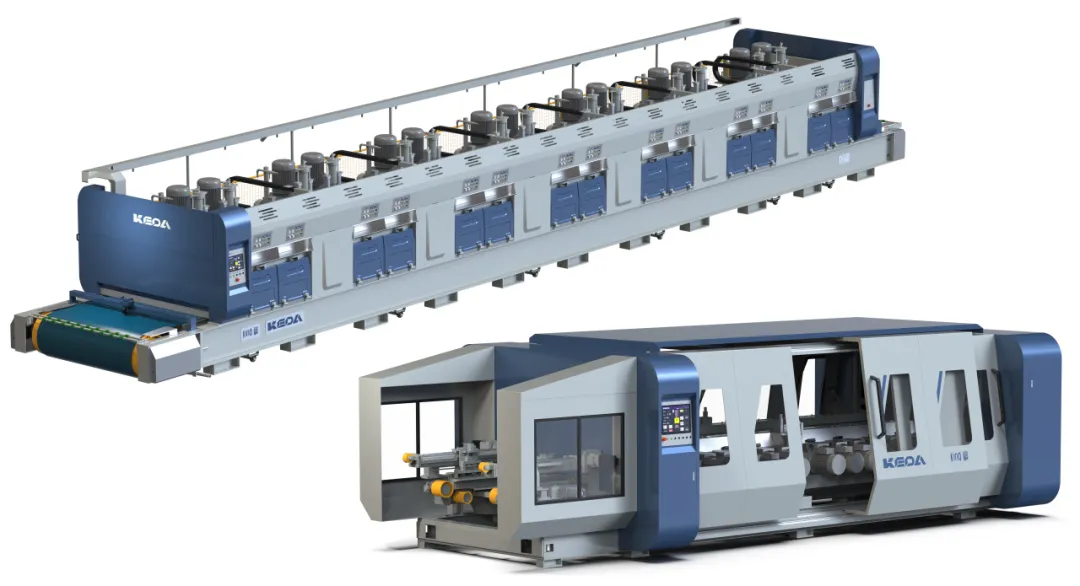
KEDA Logistics Machinery Division focuses on achieving intelligent & flexible production throughout the entire ceramic manufacturing process, from green bodies to finished products. This year's highlights include various combinations of AGV applications, such as the AGV + BOX pre-kiln compensator system and the AGV + sponge suction cup loading/unloading machine after-kiln storage system. Customized storage and logistics solutions are provided based on different site conditions.
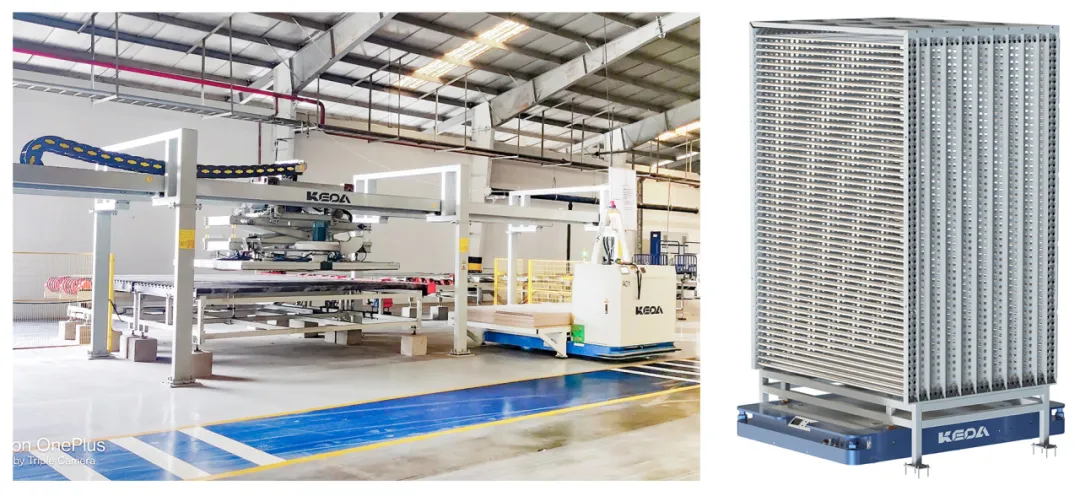
KEDA Sorting & Packaging Machinery Division introduces the newly designed KEDA KING Series rapid production transfer packaging machine, capable of achieving a packaging speed of up to 15.8 packs/minute (400×800mm). Featuring multiple patented technologies from KEDA, the machine offers multi-level parameter displays, efficient edge computing, and seamless integration with the KEDA OS system. It delivers stronger functionality and more intelligent, user-friendly operation.

▶ Diverse Services Creating Multi-Dimensional Value for Customers
With the advancement of KEDA's "Global Ceramic Production Service Provider" strategy, KEDA Ceramic Machinery is developing a new dual-engine model driven by both manufacturing & services.
KEDA Spare Parts & Service Division will showcase high-quality spare parts & consumables, complete production line machinery maintenance & refurbishment, and after-kiln production line operation & maintenance contracting services. Currently, more than 40 contracting projects are operating efficiently and stably in both China and international markets, significantly reducing customers' operational costs and ensuring product quality.
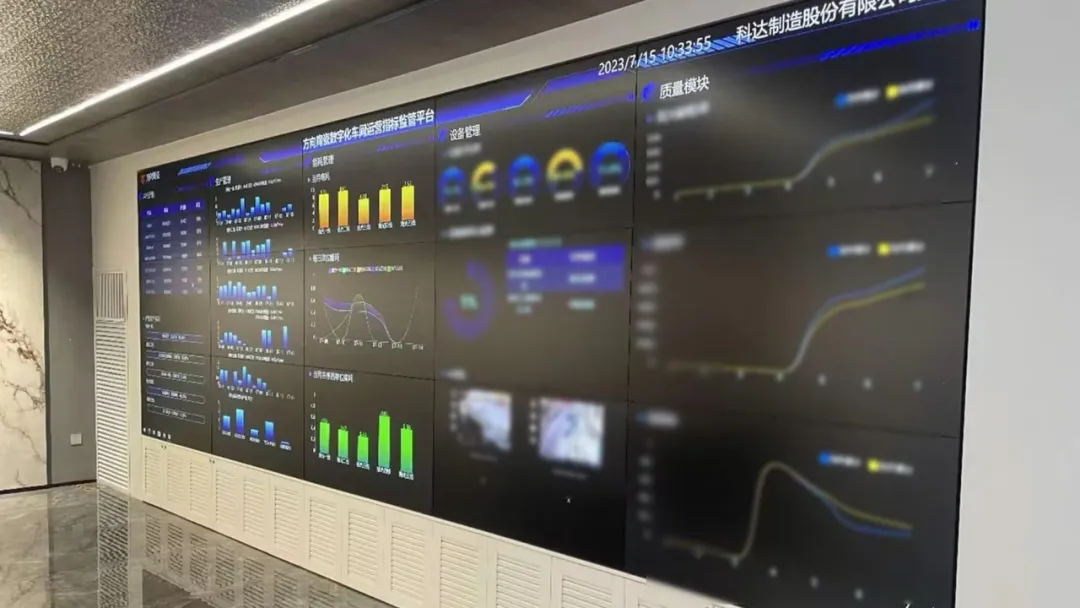
The KEDA Digital Factory System (CeramiX IMCS, formerly known as Zhentao MOM) includes 8 core functional modules covering production data acquisition, machinery operation parameter monitoring, machinery status monitoring, fault warnings, and more. It also integrates AI-assisted process quality decision-making functions, effectively reducing labor and management costs, improving operational efficiency, and accelerating the digital transformation of production management. The system provides an optimal solution for intelligent manufacturing upgrades in the ceramic industry.
HLT&DLT: Smart Future, Green World
HLT&DLT focuses on the research, development, and manufacturing of ceramic raw material machinery with a commitment to energy conservation, environmental protection, intelligence, and efficiency, providing vital support for the transformation and upgrading of ceramic enterprises worldwide. The high-capacity PST45000 energy-saving and eco-friendly spray system integrates features such as energy efficiency, environmental protection, intelligence, high output, and compact footprint. It can achieve a maximum daily powder output of up to 2,500 tons.
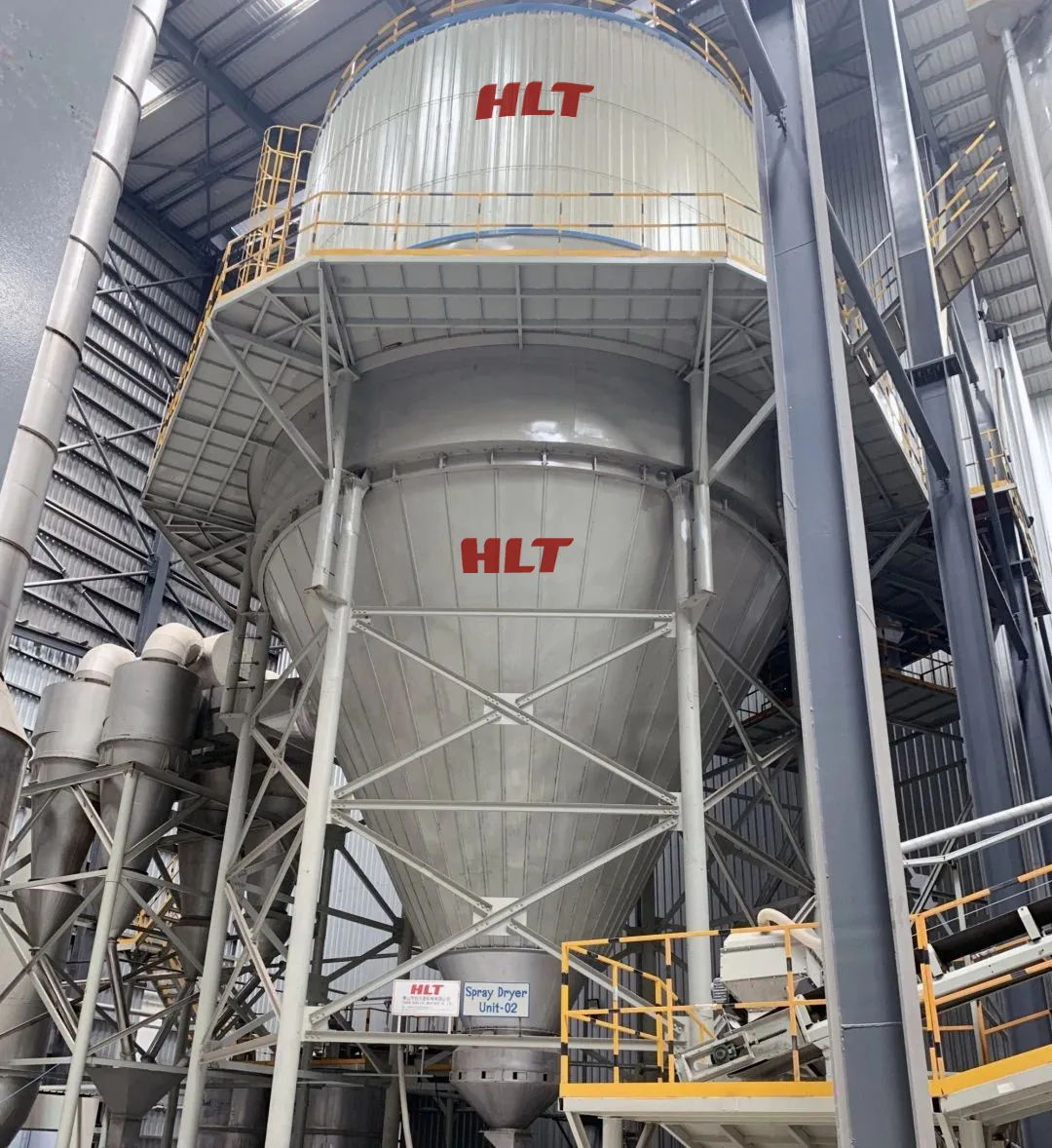
The digital, energy-saving continuous ball milling system includes multiple management modules such as automatic batching and feeding, machinery monitoring, energy consumption analysis, production reporting, and mobile app data monitoring. The system is user-friendly and easy to operate, with one-click startup functionality.
The fully automatic glazing system, with an annual capacity of 100,000 tons, supports fully enclosed operations with automated metering, proportioning, feeding, and mixing. It ensures a clean working environment with zero leakage or pollution and zero material waste.
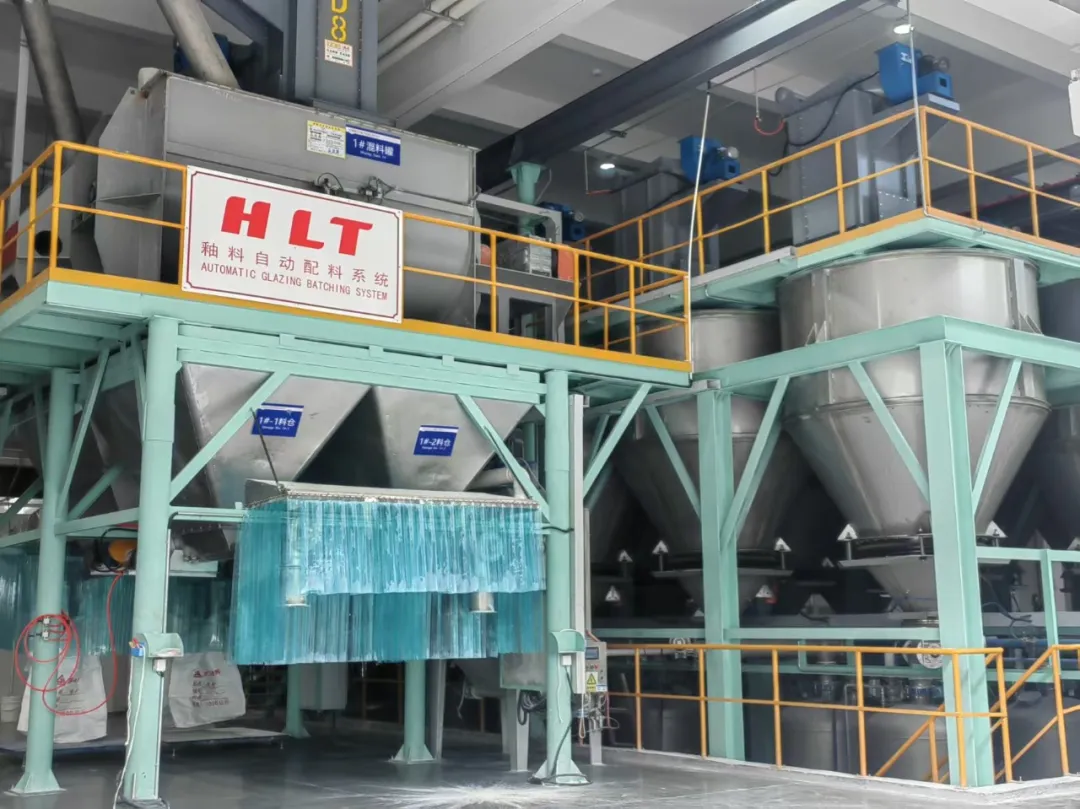
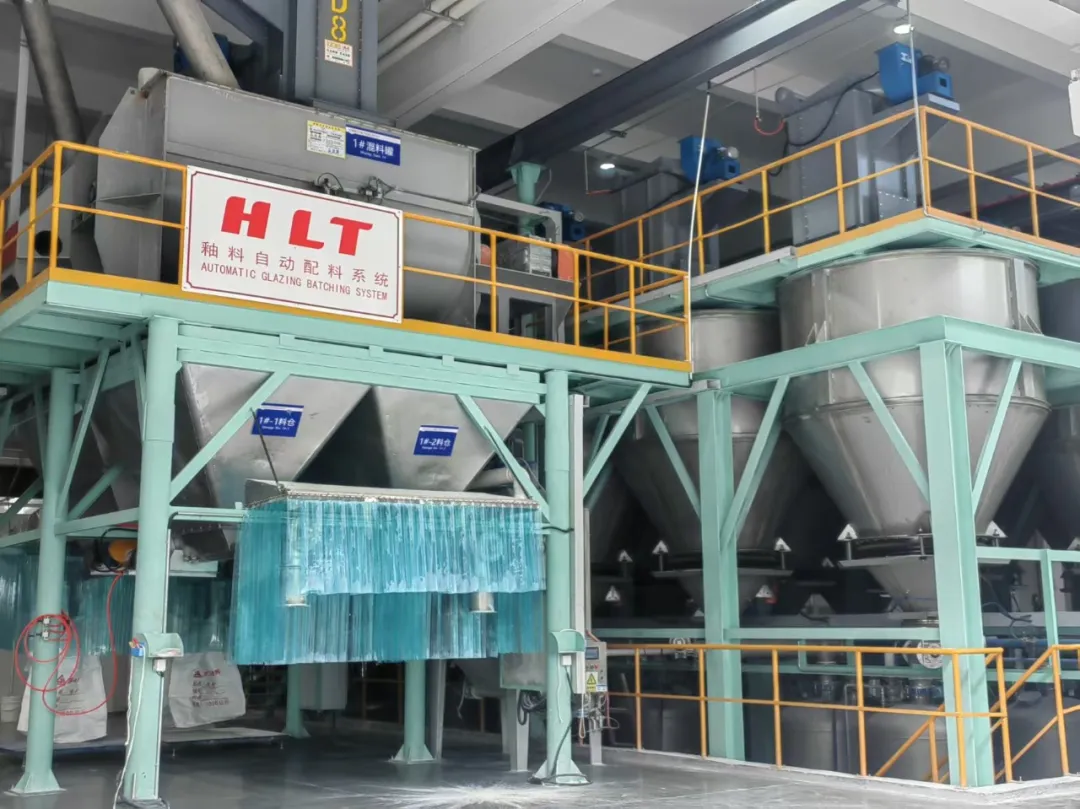
▶ Customized Production Solutions with Continuous Roll Forming System
HLT&DLT has launched the new HR1600 & HR1800 continuous roller presses, designed to offer comprehensive production optimization for ceramic enterprises through innovative engineering:
The continuous roller compaction process allows for unrestricted green body dimensions with minimal deviations and superior quality. Validated through stable and continuous production at speeds exceeding 10m/min, the HR series presses deliver high pressing speeds & outputs, significantly enhancing productivity.
The presses also offer stable & reliable performance, simple adjustment, and flexible green body cutting to meet the demands of efficient customized production. The rapid changeover capabilities enable fast responses to market fluctuations. Moreover, the production line reduces labor dependency, lowers costs, and enhances production stability & consistency with a high degree of automation. The intelligent control system enables remote monitoring and fault warning, further improving production management capabilities.
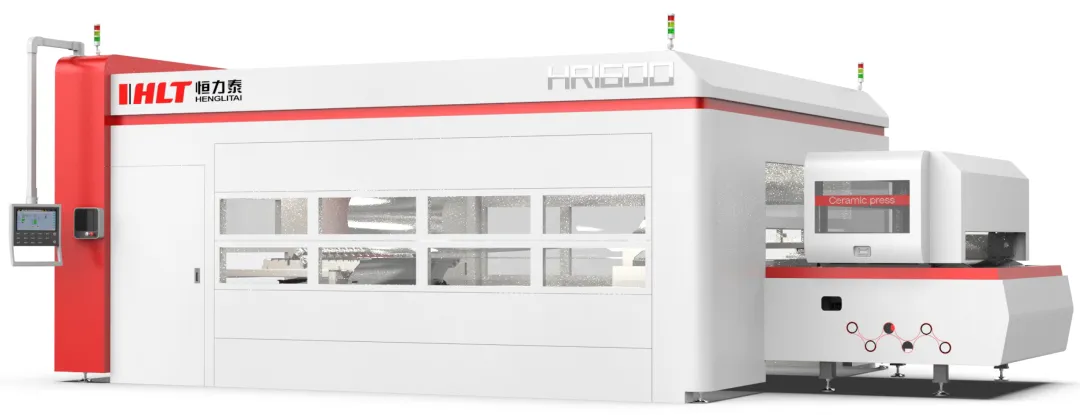
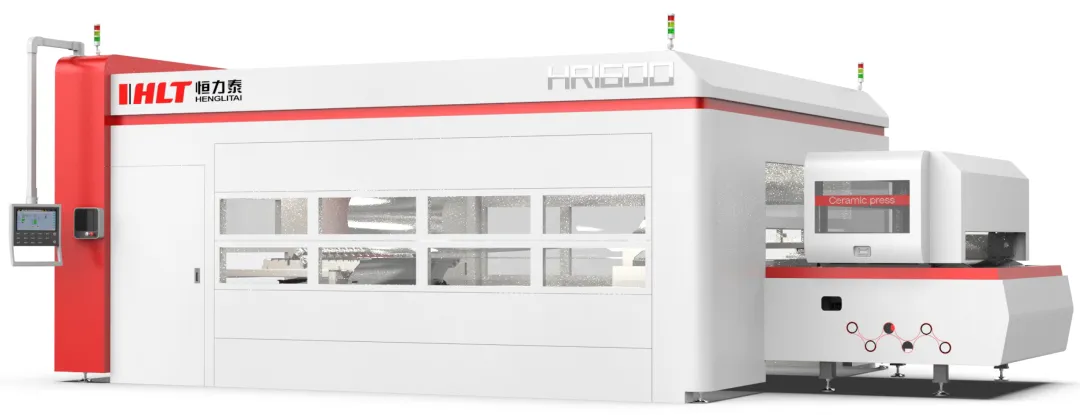
▶ New Zero-Carbon Combustion Technology: Pioneering a Green Future for the Ceramic Industry
The "World's First Demonstration Production Line for Ceramic Industry Ammonia-Hydrogen Zero-Carbon Combustion Technology" officially began operations on September 26, 2024, at the Monalisa Foshan Production Base. The "Ammonia-Hydrogen Zero-Carbon Combustion Kiln", upgraded by DLT, spans 150 meters in length with an annual production capacity of 1.5 million square meters. Using 100% pure ammonia as fuel, it directly eliminates carbon dioxide emissions, making it a true "zero-carbon industrial kiln".
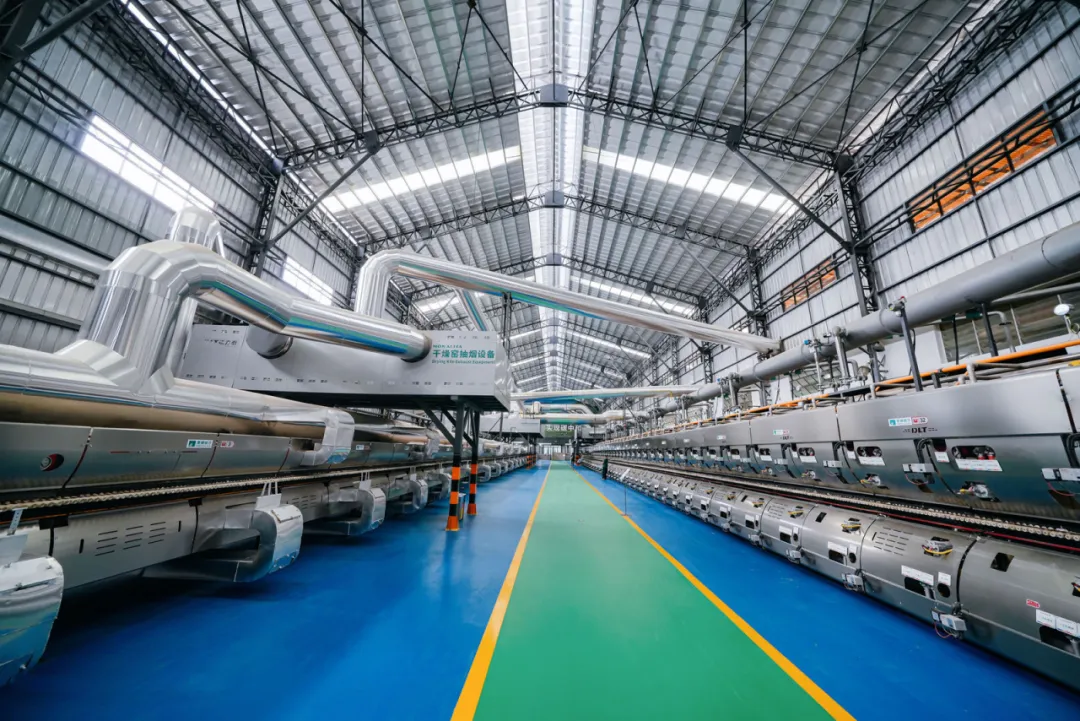
This demonstration production line not only validates the feasibility of applying "Ammonia-Hydrogen Zero-Carbon Combustion Technology" in large-scale production and continuous industrial kilns, but also provides ceramic enterprises with a replicable zero-carbon manufacturing solution. It supports the integration of ammonia-hydrogen new energy technologies and provides valuable technical support and data accumulation. Additionally, it introduces new technologies, standards, and demonstrations to reduce carbon emissions in the building ceramic industry.
▶ Intelligent Whiteware Complete Production Line Supporting Ceramic Enterprise Transformation
The roller kiln for tableware launched by HLT&DLT is suitable for various heat treatment processes such as bisque firing, glazing, and decoration firing of tableware. It features a wide temperature control range, high output, low energy consumption, and an extended automatic temperature control range. The optimal energy consumption is 950kcal/kg.c. Customized firing solutions can be provided based on product process requirements, including reactive glazes, crackled glazes and snowflake glazes.
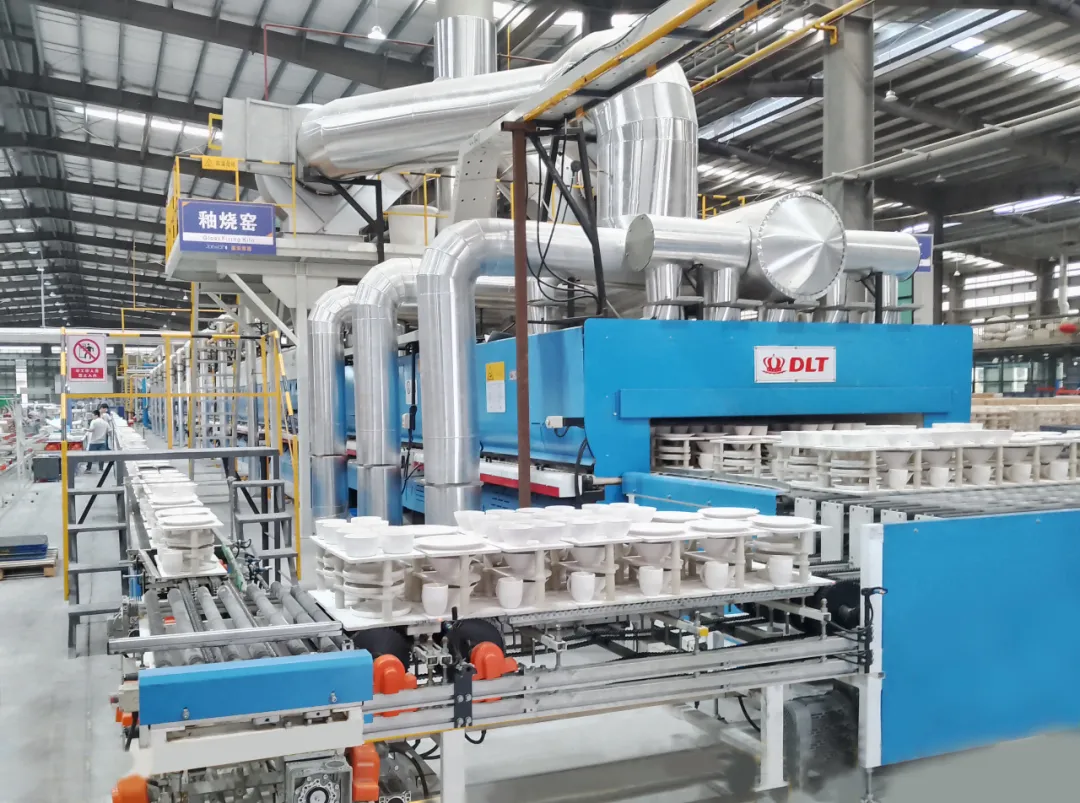
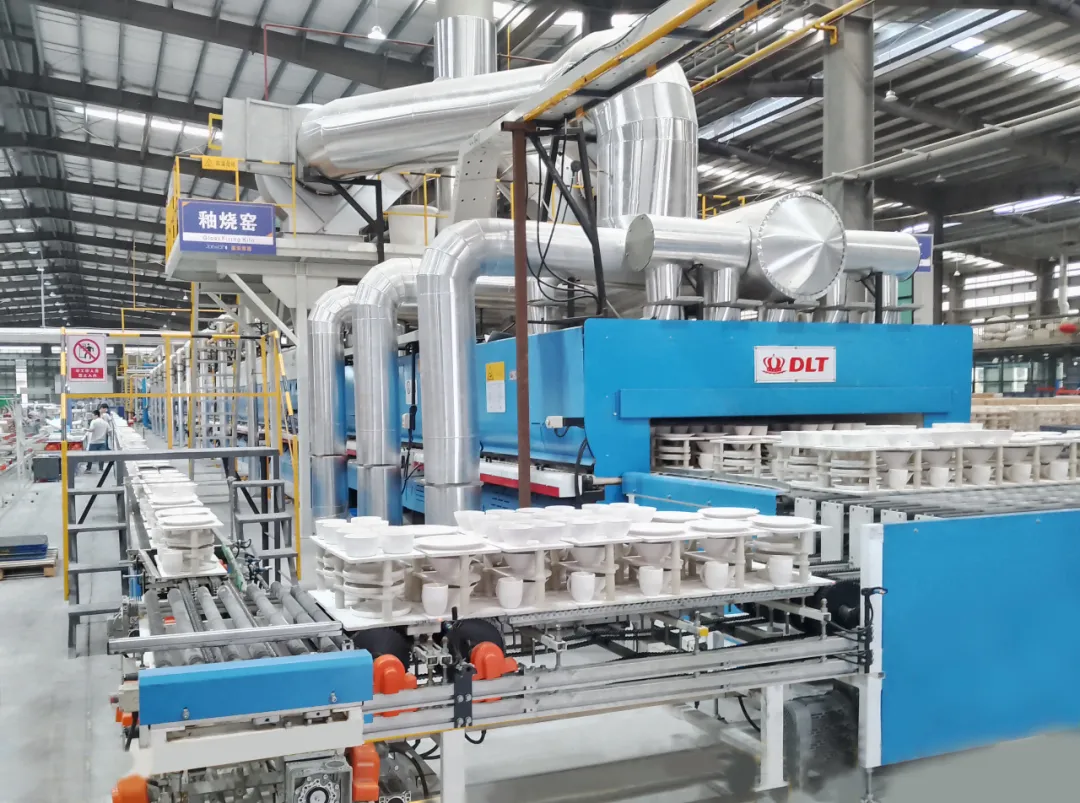
At this exhibition, the sanitary ware complete line digital twin system will be showcased, which utilizes 3D modeling and real-time data visualization to present complex production processes in an intuitive manner. This technology not only enhances production flexibility and efficiency but also provides strong support for sustainable development. Other products, including tunnel firing kilns, intelligent drying & storage systems, and automatic rolling forming production lines, will also be featured.
ICF & Welko: Global Partners in Ceramic Excellence
As a long-standing leader in spray drying technology, ICF & Welko has recently incorporated advanced design tools into its technical framework. Leveraging these tools, ICF & Welko conducted CFD (Computational Fluid Dynamics) simulations on the spray dryer's core component—the advanced slurry distribution system.
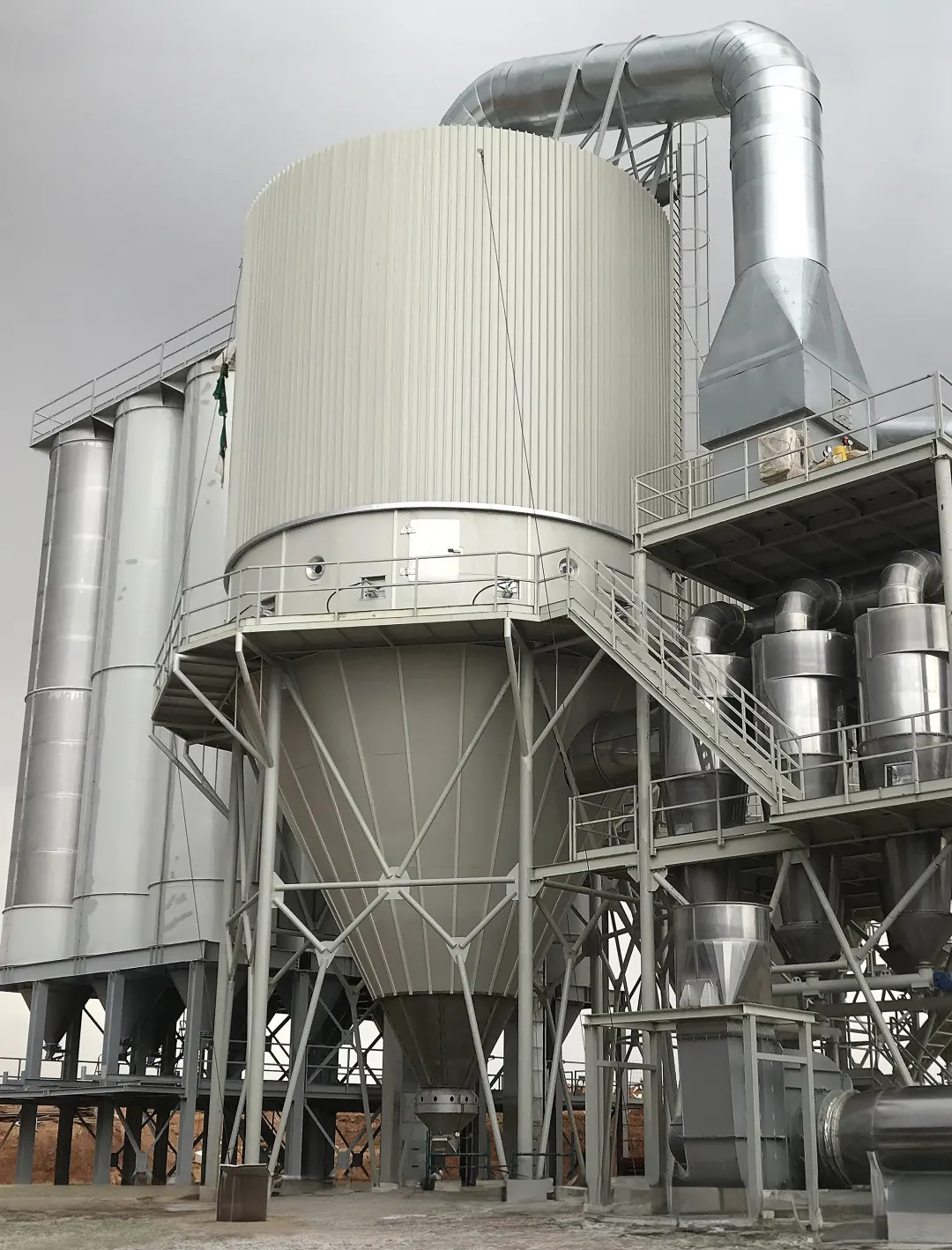
These simulations allowed for optimization of the fin contour design, significantly improving the hot airflow distribution within the drying chamber. As a result, the heat exchange efficiency between the hot air and the atomized ceramic slurry has been greatly enhanced, leading to a comprehensive improvement in overall machinery performance.
The system includes:
- Heat exchangers on kiln exhaust gases to preheat the air for dryers, eliminating energy consumption in this phase.
- Recovery of hot air from kiln cooling to feed the burners, combined with a new modulated air-gas combustion system, improving combustion and reducing fuel use.
- Reuse of heat from kiln cooling: The recovered air is sent to both horizontal and vertical dryers.
- Integration with the spray dryer: An additional flow of recovered hot air is directed to the spray dryer and mixed with exhaust gases from the gas turbine.
At the 2025 Foshan Uniceramics Expo, ICF & Welko will share the evolution of our technologies, presenting versions in advanced development designed to meet the needs of a sector increasingly oriented toward decarbonization:
- WFRE-MH: Kiln using gas-hydrogen mixtures, designed to reduce greenhouse gas emissions by replacing carbon in natural gas with water vapor.
- WFRE-L: Fully electric kiln, suitable for smaller installations, eliminates combustion products, and minimizes greenhouse gas emissions.
- WFRE-Hybrid: Solution combining fuel preheating (gas or gas-hydrogen mixtures) with electric firing, offering maximum efficiency with reduced environmental impact.
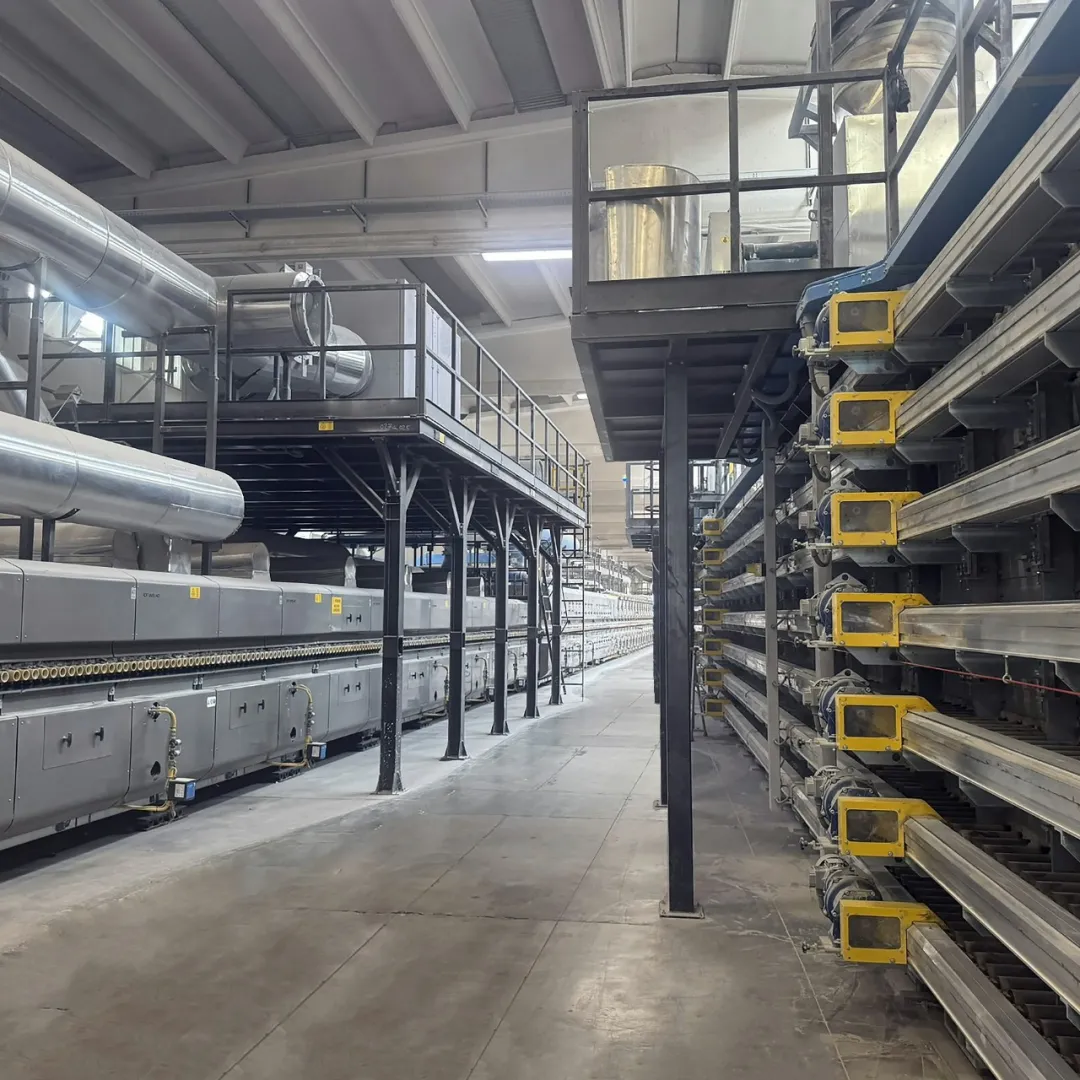
F.D.S. Ettmar is a European ceramic tile mold manufacturer founded in 1992 in Sassuolo, Italy. Its business includes R&D, manufacturing, and refurbishment of various ceramic pressing molds, covering a wide range of ceramic tile mold models from 30×60 cm to 60×180 cm.
The entering punches moulds will be highlighted at the show. This is a very simple mould which allows to increase production in the press. It makes easy the ceramic production with any kind of powder: porous, stoneware or porcelain body. At the same time, you can also produce different tile thickness in the same mould.
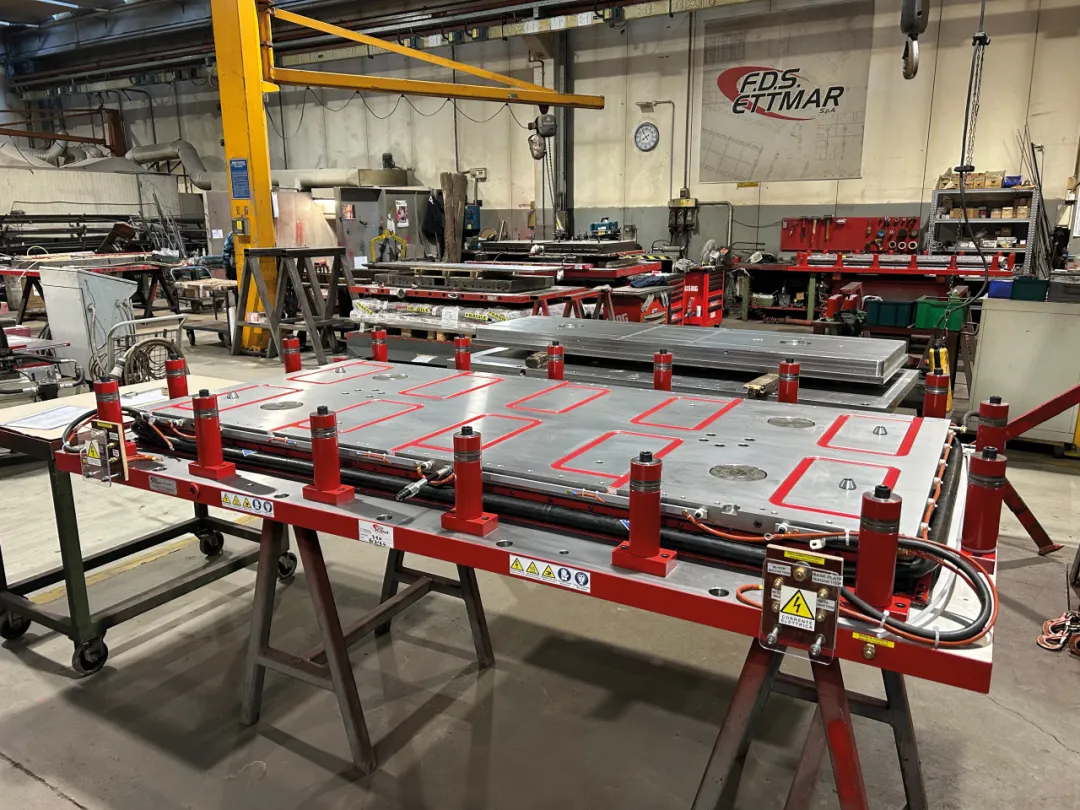
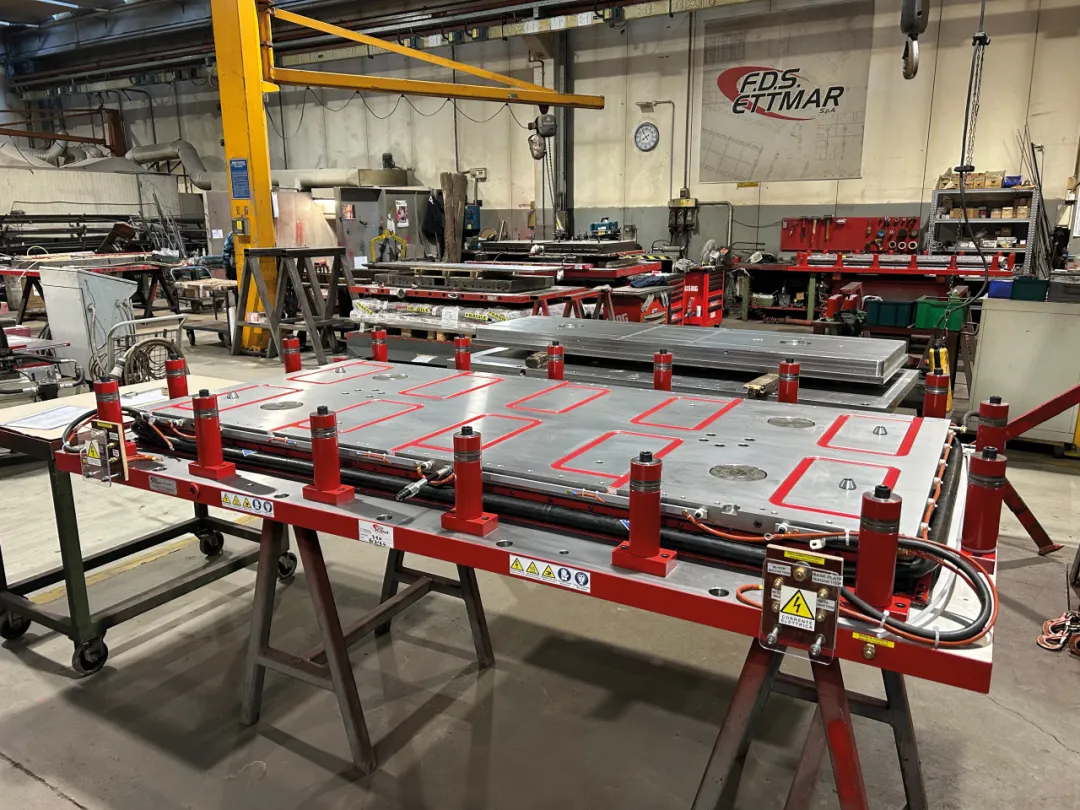
Quanitech: When It Comes to Ink, Stability is Everything
At this year's Foshan Uniceramics Expo, Quanitech will showcase a range of innovative technologies and products, including its Dry Granule Positioning Technology and Digital Micro-Carving, helping customers create more expressive & competitive ceramic designs.
Among them, the Dry Granule Positioning Technology stands out as a groundbreaking tile decoration process. It cleverly uses an inkjet printer to apply digital adhesive, which precisely bonds dry granules through its viscosity, creating unique localized decorative effects and expanding the creative possibilities in tile design.
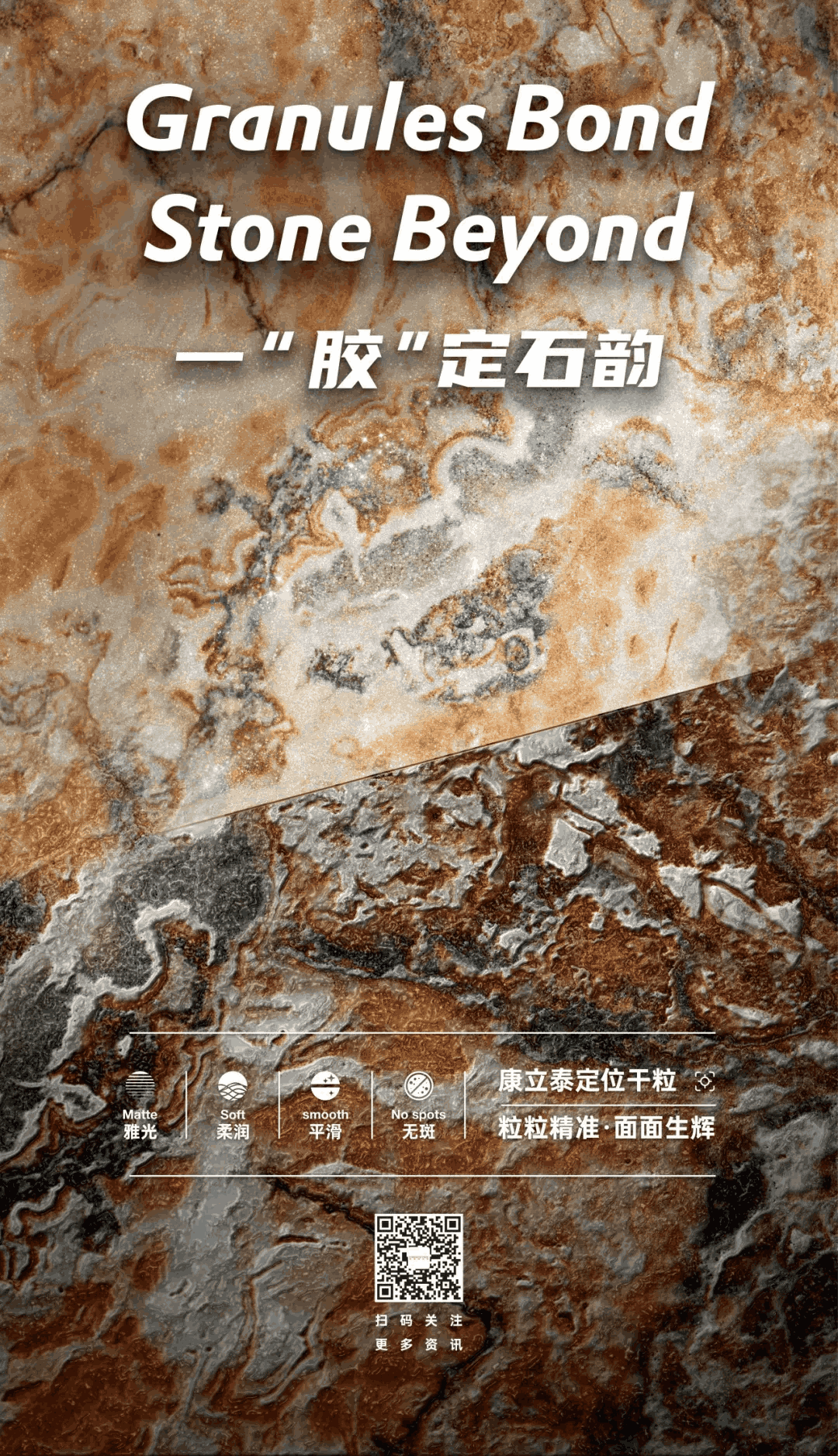
Digital Micro-Carving offers a next-generation digital mold solution that replaces traditional dry granules, digital molds, and body molds. It retains the tactile texture of granules and preserves detailed linework. Compared to conventional mold technologies, this solution resolves the alignment challenge between patterns & molds during production, delivering more realistic & natural decorative effects.
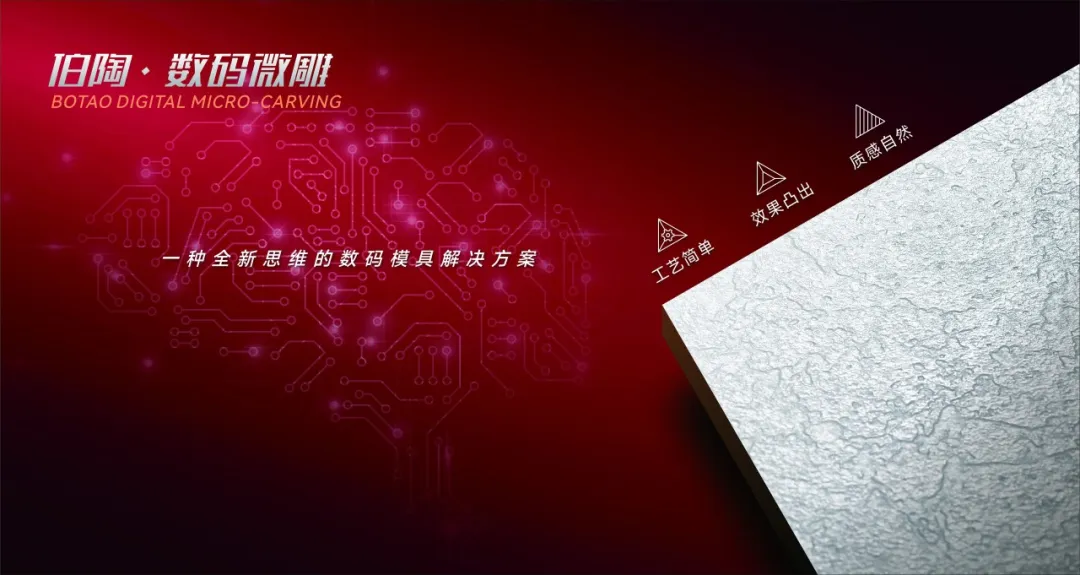
KEDA Stone Machinery: Pioneering Complete Production Line Machinery & Technology for Cement Based Artificial Stone
At this exhibition, KEDA Stone Machinery will focus on showcasing its Artificial Stone Complete Production Line Machinery & Technological Solutions, fully demonstrating its industry-leading capabilities in digital manufacturing.
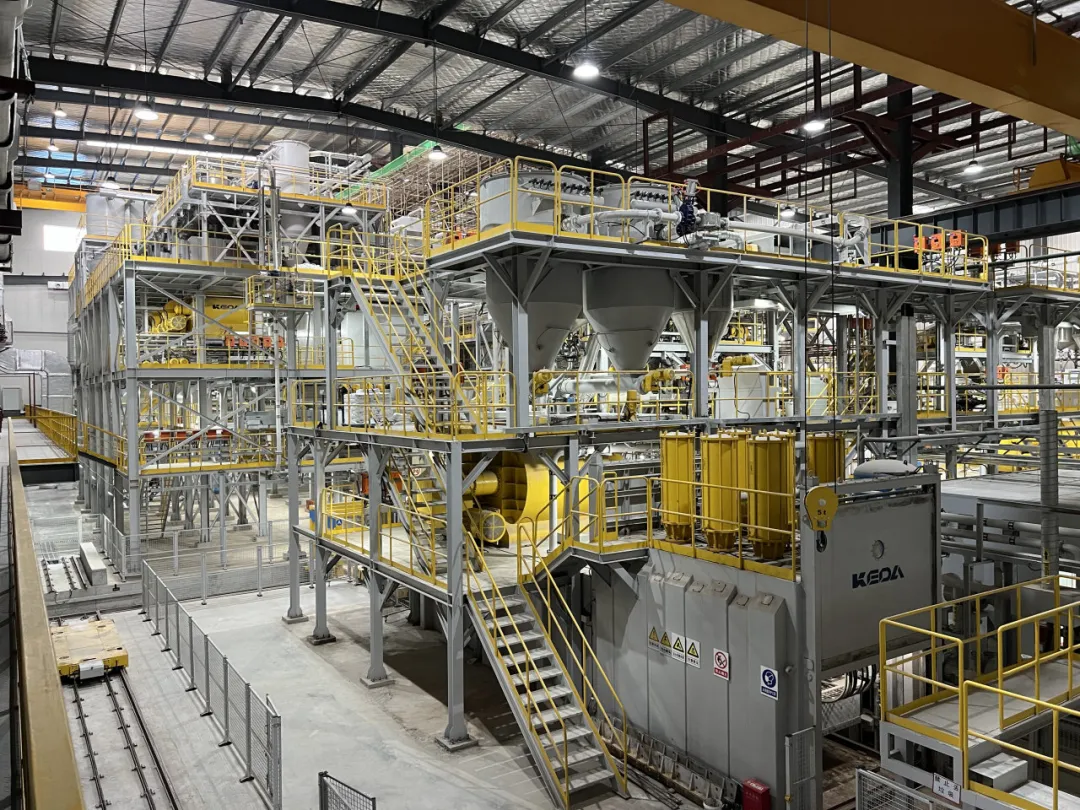
This project has successfully developed the World's First Complete Production Line for Cement Based Artificial Stone, integrating multiple breakthrough technologies such as a color fabric system, intelligent conveyor modules, core pressing process, and automated demoulding system. It enables full-process visual management of production, reducing energy consumption by 30% and increasing capacity by 40% through a digital control platform.
KEDA SUREMAKER: Launching Multiple Innovative AAC Technologies and Products
At this year's expo, KEDA SUREMAKER will spotlight its latest advances in Autoclaved Aerated Concrete (AAC), including green cake separating technology, BIM-based design, and steam-saving solutions.
The newly self-developed AAC Green Cake Separating Solution adopts a vertical cutting–green cake separating–horizontal steam curing process. To optimize this workflow, KEDA SUREMAKER has engineered a specialized green cake smart separating machine designed to enhance production efficiency while ensuring precise & smooth separation.
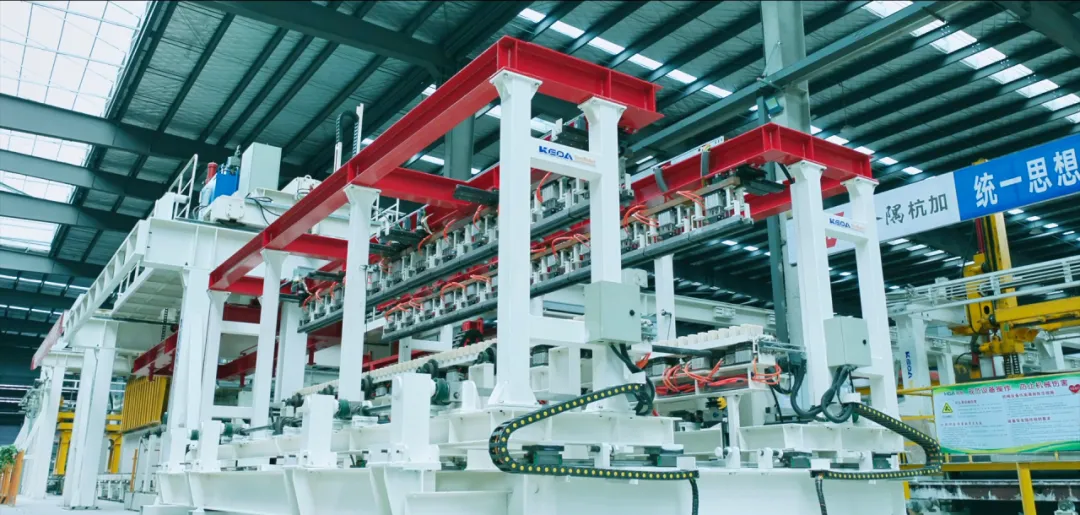
The BIM Design Technology with visual design capabilities has already been implemented in the early planning and design stages of several AAC projects, significantly enhancing the customer experience throughout the construction cycle.
The EcoSteam Steam-Saving Technology integrates automatic steam distribution, automatic drainage, and waste heat recovery. This all-in-one solution is set to revolutionize steam utilization in AAC production, effectively addressing long-standing energy efficiency challenges.
(KEDA Industrial Group)